Compact sensor sets the stage for a detailed exploration of these remarkable devices. They are finding increasing applications across diverse industries due to their size, efficiency, and performance capabilities.
This comprehensive guide delves into the intricacies of compact sensors, examining their design, manufacturing, performance metrics, and practical applications. From their fundamental characteristics to advanced integration methods, we will cover every aspect.
Introduction to Compact Sensors
Compact sensors are a specialized class of sensors designed for space-constrained applications. They offer a balance between performance and size, making them suitable for various industries, from consumer electronics to industrial automation. Their small form factor allows for integration into intricate systems, contributing to miniaturization and improved functionality.Compact sensors are distinguished from other sensor types primarily by their reduced physical dimensions.
This characteristic allows for their integration into tight spaces and complex systems, often with specific design constraints and performance tradeoffs. Key performance characteristics, such as sensitivity, accuracy, and response time, might be slightly modified to accommodate the reduced size and complexity.
Types of Compact Sensors
Various types of compact sensors exist, each tailored for specific applications. These include, but are not limited to, compact pressure sensors, temperature sensors, and proximity sensors. The specific type chosen depends on the particular requirements of the application, balancing size, performance, and cost.
Examples of Compact Sensors
- Compact Pressure Sensors: These sensors are crucial for monitoring pressure in confined environments. They find applications in automotive systems, such as tire pressure monitoring systems, and in industrial settings, where precise pressure readings are needed in small spaces. A typical example might be a miniature pressure sensor integrated into a fuel injection system.
- Compact Temperature Sensors: These sensors are widely used in consumer electronics and industrial processes. They measure temperature in tight spaces and are vital for maintaining optimal operating conditions in a variety of systems. Examples include temperature sensors used in smartphones or wearable devices for thermal management.
- Compact Proximity Sensors: These sensors detect the presence of an object without physical contact. They are frequently employed in automated assembly lines, robotic systems, and other applications requiring non-contact object detection. A good example is a compact proximity sensor used in a smart home system for automatically adjusting lights based on presence.
- Compact Optical Sensors: These sensors measure physical parameters by detecting light. Applications include measuring liquid levels in containers, detecting the presence of objects, or monitoring environmental conditions. Examples include compact optical sensors for detecting the presence of a user’s hand in a touch-screen interface.
Comparative Analysis of Compact Sensor Types
Sensor Type | Application | Size | Key Features |
---|---|---|---|
Compact Pressure Sensor | Automotive (tire pressure), Industrial (process control) | Small, typically < 10 mm3 | High accuracy, low power consumption, fast response time |
Compact Temperature Sensor | Consumer electronics (smartphones), Industrial (process monitoring) | Very small, often < 5 mm3 | High sensitivity, wide temperature range, excellent stability |
Compact Proximity Sensor | Automated assembly, robotics, security systems | Very compact, typically < 20 mm3 | Non-contact detection, fast response time, reliable operation in harsh environments |
Compact Optical Sensor | Liquid level measurement, object detection, environmental monitoring | Compact, varying depending on the application | Light-based sensing, high precision, suitable for non-invasive measurements |
Applications of Compact Sensors
Compact sensors, due to their small size, low power consumption, and often low cost, have found widespread application across diverse industries. Their portability and ease of integration make them valuable tools for a variety of tasks, from monitoring environmental conditions to controlling industrial processes. This versatility is crucial in modern technology where efficiency and miniaturization are highly sought after.
Industrial Automation
Compact sensors play a vital role in industrial automation by enabling precise control and monitoring of machinery and processes. Their ability to detect various parameters, such as position, proximity, and temperature, is critical for maintaining optimal performance and safety. For example, in assembly lines, compact sensors detect parts, ensuring accurate placement and preventing errors. In robotic systems, sensors detect obstacles, enabling safe navigation and avoiding collisions.
The real-time data collection capabilities of these sensors are essential for real-time process adjustments.
Environmental Monitoring
Compact sensors are frequently used in environmental monitoring applications. Their portability and low power consumption allow for deployment in remote locations or areas with limited access. They are utilized for measuring various environmental parameters, including temperature, humidity, and air quality. For example, in weather stations, compact sensors provide data on atmospheric conditions, while in agricultural settings, they monitor soil moisture levels, enabling informed irrigation practices.
The ability to deploy numerous sensors across large areas is beneficial for comprehensive environmental monitoring.
Medical Diagnostics
Compact sensors are finding increasing applications in medical diagnostics, particularly in portable medical devices. Their ability to measure physiological parameters, such as blood pressure, heart rate, and glucose levels, makes them valuable tools for early detection of health issues. Examples include wearable devices that track activity and vital signs. These sensors contribute to remote patient monitoring, which is especially important in areas with limited access to healthcare facilities.
Miniaturization and integration of these sensors in devices like blood glucose meters lead to more user-friendly and efficient diagnostic tools.
Automotive Industry
Compact sensors are used in the automotive industry for various functions, such as safety and performance enhancement. Their ability to detect objects, measure distances, and monitor vehicle conditions contributes to accident prevention and improved driving experience. Examples include sensors for adaptive cruise control, parking assistance systems, and collision avoidance. The reliability and durability of compact sensors are essential in harsh automotive environments.
Table: Summary of Compact Sensor Applications
Application | Sensor Type | Advantages |
---|---|---|
Industrial Automation | Proximity, Position, Temperature | Precise control, real-time data, safety enhancements |
Environmental Monitoring | Temperature, Humidity, Air Quality | Portability, remote deployment, comprehensive data |
Medical Diagnostics | Blood Pressure, Heart Rate, Glucose | Early detection, remote patient monitoring, user-friendly |
Automotive Industry | Proximity, Distance, Vehicle Conditions | Accident prevention, improved driving experience, performance enhancement |
Design Considerations for Compact Sensors
Minimizing size and weight while maintaining performance is crucial for compact sensor design. This necessitates careful consideration of various factors, including material selection, power consumption, and accuracy requirements. Engineers must balance these competing demands to create sensors that are both effective and portable.The design of compact sensors requires a delicate balance between achieving miniaturization and ensuring the desired performance characteristics.
Compact sensors are becoming increasingly crucial in various applications. Their small size and efficiency are key advantages, but their performance often hinges on the underlying storage technology. For instance, a comparison of HDDs, as seen in the HDD comparison , can offer insights into how different storage options affect overall system performance, which in turn impacts the compact sensor’s overall capabilities.
This involves understanding and managing trade-offs between critical parameters such as size, weight, accuracy, and power consumption. Different applications demand varying levels of performance, necessitating tailored design approaches.
Material Selection
Material selection plays a significant role in achieving compactness. Lightweight and robust materials are crucial for minimizing the sensor’s physical footprint. Choosing appropriate materials is essential to ensure the sensor’s structural integrity and performance in the intended environment. Examples include polymers, composites, and advanced ceramics. Their specific properties, such as density, strength, and electrical conductivity, dictate the sensor’s performance and suitability for various applications.
Minimizing Size and Weight
Techniques for minimizing sensor size and weight often involve innovative design approaches. Microfabrication and MEMS (Microelectromechanical Systems) technologies are frequently employed. These technologies enable the creation of intricate structures with extremely small dimensions, enabling the integration of multiple sensor components onto a single chip. This approach reduces overall size and weight significantly, making the sensor more portable and suitable for diverse applications.
Furthermore, optimizing the layout of components and carefully selecting the mounting methods are critical aspects in achieving the desired miniaturization.
Accuracy and Power Consumption Trade-offs
There’s a fundamental trade-off between achieving high accuracy and minimizing power consumption in compact sensor design. More complex sensor structures and advanced signal processing algorithms often demand more power. Conversely, simplified designs may result in lower accuracy. The specific application will dictate the acceptable level of accuracy and power consumption. Engineers must carefully weigh these factors to arrive at a design that balances performance with portability.
For example, in wearable health monitoring devices, power consumption is a critical factor, whereas in high-precision industrial sensors, accuracy might take precedence.
Design Considerations Table
Design Consideration | Potential Challenges | Solutions |
---|---|---|
Size and Weight Minimization | Compromising structural integrity and performance | Employing lightweight materials, optimizing component layout, using microfabrication techniques. |
Accuracy | Reduced sensitivity due to smaller components | Using high-precision materials and calibration techniques, improving signal processing algorithms. |
Power Consumption | Difficulty in providing sufficient power to smaller sensors | Optimizing power management circuits, employing low-power components, and energy harvesting techniques. |
Environmental Factors | Sensitivity to temperature, humidity, or vibrations | Using appropriate shielding, implementing robust packaging, and using materials with improved stability. |
Manufacturing Processes for Compact Sensors
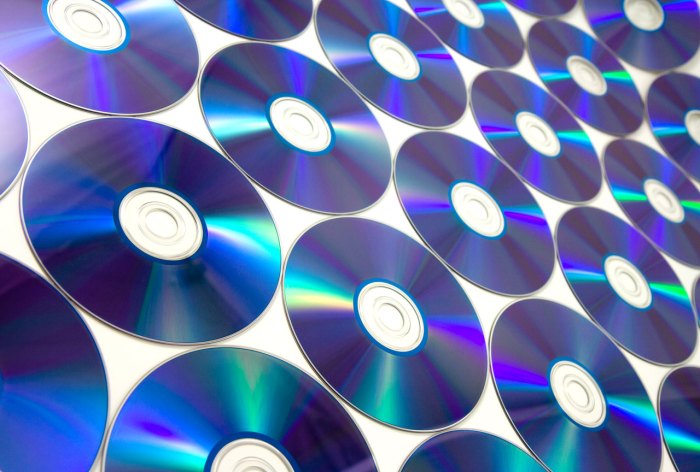
Manufacturing compact sensors demands meticulous precision and a variety of techniques tailored to the specific sensor type and material properties. These techniques must balance the need for small size with the required performance characteristics, such as sensitivity, accuracy, and stability. The choice of fabrication method significantly impacts the final sensor’s cost, complexity, and ultimately, its suitability for diverse applications.
Microfabrication Techniques
Microfabrication techniques are prevalent in the creation of compact sensors. These methods leverage lithographic processes to pattern materials at the microscale, enabling the precise creation of intricate sensor structures. The use of photolithography, etching, and deposition allows for the fabrication of complex microstructures, enabling the integration of multiple sensor components onto a single chip.
Different Fabrication Methods for Various Sensor Types
The choice of fabrication method depends heavily on the specific sensor type and its required performance characteristics. For instance, piezoelectric sensors, which rely on the material’s ability to generate an electrical charge when mechanically stressed, often benefit from micromachining techniques to create the necessary microstructures for enhanced sensitivity and stability. Conversely, optical sensors, which utilize light to measure physical parameters, often leverage techniques like thin-film deposition to precisely control the optical properties of the sensor components.
Comparison of Fabrication Methods
Manufacturing Process | Materials | Advantages |
---|---|---|
Micromachining | Silicon, polymers, metals | High precision, complex structures, relatively low cost for simple designs. |
Thin-film deposition | Various materials (metals, oxides, semiconductors) | Precise control over material properties, suitable for optical and electrochemical sensors. |
3D printing | Polymers, conductive inks, composites | Rapid prototyping, customized designs, potentially lower cost for certain applications, versatile. |
MEMS (Microelectromechanical Systems) | Silicon, polymers, metals | Integration of multiple components, high sensitivity, compact size, potential for miniaturization. |
Steps Involved in Micromachining, Compact sensor
The micromachining process typically involves several key steps: First, a silicon wafer is prepared. Then, photolithography is used to pattern the wafer with a photoresist, defining the desired sensor structure. Subsequent etching steps remove the unwanted material, creating the precise microstructures. Finally, the sensor components are integrated, and the protective layers are deposited. These steps are crucial in ensuring the structural integrity and functional performance of the resulting sensor.
Steps Involved in Thin-Film Deposition
Thin-film deposition techniques, such as sputtering and chemical vapor deposition (CVD), involve depositing thin layers of materials onto a substrate. The precise control over the thickness and composition of the deposited layers is essential for optimizing the sensor’s performance. Furthermore, these techniques are often used to create multi-layered structures with tailored optical or electrical properties.
Performance Metrics of Compact Sensors
Compact sensors, due to their miniature size and often specialized functionalities, necessitate a comprehensive evaluation of their performance. A multitude of metrics, considered in conjunction, provide a holistic understanding of the sensor’s capabilities and limitations. These metrics are critical for ensuring the sensor meets the requirements of its intended application and for comparing different sensor models.
Compact sensors are becoming increasingly important in various applications. Their small size and efficiency are key advantages, but their performance can be affected by factors like power consumption. The latest advancements in RAM 2025 are showing promise for optimizing compact sensor design, particularly in reducing power consumption. This should lead to even more sophisticated and versatile compact sensors in the future.
Key Performance Metrics
Various performance metrics are used to assess the quality and suitability of compact sensors. These metrics encompass a wide range of characteristics, from accuracy and precision to response time and stability. Understanding these metrics is vital for effective selection and integration of the sensor into a system.
Accuracy and Precision
Accuracy reflects how close a sensor’s measured value is to the true value. Precision quantifies the repeatability of measurements. High accuracy and precision are desirable for critical applications, where small errors can have significant consequences. For example, in industrial automation, precise measurements are essential for maintaining product quality and efficiency. Errors can lead to wasted materials, defective products, or even safety hazards.
Sensitivity and Resolution
Sensitivity measures how much the sensor’s output changes in response to a change in the measured quantity. Resolution quantifies the smallest detectable change in the measured quantity. High sensitivity and resolution are essential for detecting subtle variations and for achieving precise measurements. In environmental monitoring, sensitivity and resolution are vital for detecting small changes in pollutant concentrations.
Response Time and Stability
Response time indicates the time it takes for the sensor to respond to a change in the measured quantity. Stability refers to the consistency of the sensor’s output over time. Fast response time and high stability are crucial for dynamic applications, where rapid and consistent measurements are necessary. In medical imaging, a sensor’s stability and response time are crucial for accurate and consistent results.
Linearity and Hysteresis
Linearity describes how well the sensor’s output follows a linear relationship with the input. Hysteresis is the difference in output values for the same input when the input is increasing versus decreasing. Linearity and low hysteresis are essential for ensuring predictable and consistent measurements. In process control systems, the linearity and low hysteresis of sensors are crucial for maintaining stable and accurate process parameters.
Environmental Factors
Environmental factors, including temperature, humidity, and pressure, can significantly impact the performance of compact sensors. Robustness against these factors is essential for reliable operation in various conditions. In harsh environments, like those found in industrial settings, sensors with high environmental resistance are vital for continued functionality and data collection.
Performance Metrics Table
Metric | Units | Significance |
---|---|---|
Accuracy | e.g., ppm, % | Closeness to true value |
Precision | e.g., standard deviation | Repeatability of measurements |
Sensitivity | e.g., mV/°C | Responsiveness to input changes |
Resolution | e.g., bits | Smallest detectable change |
Response Time | e.g., ms | Time to respond to changes |
Stability | e.g., % change/year | Consistency over time |
Linearity | e.g., % | Degree of output’s linear relationship to input |
Hysteresis | e.g., % | Difference in output for same input in increasing/decreasing |
Power Consumption in Compact Sensors
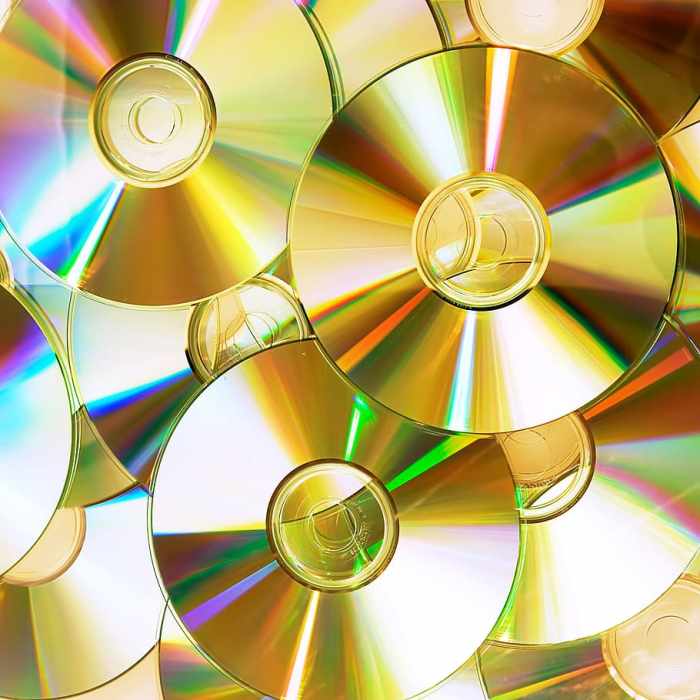
Power consumption is a critical factor in the design and application of compact sensors. Minimizing power usage is paramount for extended operational autonomy, particularly in battery-powered or resource-constrained environments. This aspect directly impacts the usability and practical deployment of these sensors in diverse applications.Power consumption directly influences the sensor’s lifespan and operational capabilities. A sensor consuming excessive power will necessitate frequent battery replacements or external power sources, which can be inconvenient, expensive, and environmentally problematic.
Efficient power management is thus essential for the widespread adoption of compact sensors.
Strategies to Minimize Power Consumption
Minimizing power consumption in compact sensors involves a multi-faceted approach. It encompasses careful selection of components, optimized circuit design, and the implementation of power-saving techniques.
- Component Selection: Choosing low-power components is crucial. This includes selecting low-power microcontrollers, analog-to-digital converters (ADCs), and power amplifiers. Selecting components with lower operational currents directly impacts the overall power consumption of the sensor.
- Circuit Design Optimization: Efficient circuit design plays a significant role. Employing techniques like power gating, sleep modes, and dynamic voltage scaling (DVS) can drastically reduce power consumption during periods of inactivity or low data acquisition rates. Proper circuit design ensures optimal energy utilization.
- Power-Saving Techniques: Implementing power-saving techniques is vital. Techniques like power gating, which temporarily disables unused circuitry, and sleep modes, which reduce the sensor’s operational frequency, can dramatically extend battery life. These techniques are especially important for applications where sensors operate intermittently.
Examples of Power-Efficient Sensor Designs
Several examples of power-efficient sensor designs exist, highlighting various approaches. These designs often leverage specialized low-power components and optimized architectures to achieve minimal power consumption.
- Wireless Sensor Networks (WSNs): WSNs are often designed with low-power sensors to extend their operational range and reduce energy consumption. Employing techniques like duty cycling, where sensors transmit data intermittently, minimizes the energy used for communication.
- Biomedical Sensors: Sensors used for biomedical applications, such as implantable devices, require extremely low power consumption to ensure long-term functionality. These sensors often leverage ultra-low-power components and advanced power management techniques.
- Environmental Sensors: Environmental sensors, frequently deployed in remote locations, often operate on battery power. Power-efficient designs are crucial to ensure sustained data collection over extended periods without frequent battery replacements.
Methods to Reduce Power Consumption
Different methods are employed to reduce power consumption in compact sensors. These methods often involve a trade-off between performance and power consumption.
Method | Description | Impact |
---|---|---|
Duty Cycling | Sensors are activated only when data acquisition is needed. | Significant power savings, but potential for data loss during inactivity periods. |
Sleep Modes | Sensor enters a low-power state when not actively measuring. | Significant power savings, but delay in response to activation. |
Power Gating | Disables unused circuitry when not needed. | Reduces power consumption during idle periods. |
Dynamic Voltage Scaling (DVS) | Adjusts the operating voltage of the sensor to match the required performance. | Optimizes power consumption for varying operational needs. |
Calibration and Testing of Compact Sensors
Accurate measurement is paramount for reliable sensor data. Calibration and testing procedures ensure compact sensors provide precise and consistent readings, vital for applications ranging from industrial automation to environmental monitoring. Proper calibration methods and performance testing are crucial to validate sensor accuracy and reliability.
Calibration Methods for Compact Sensors
Calibration establishes a relationship between the sensor’s output and the corresponding input quantity. Different methods cater to various sensor types and applications. Common methods include:
- Standard Reference Sources: Utilizing traceable reference standards, like known weights or temperature baths, to calibrate the sensor under controlled conditions. This approach ensures the sensor’s output aligns with known values, ensuring accuracy and reliability.
- Multi-point Calibration: Calibrating the sensor at multiple points within its operating range. This method helps determine the sensor’s linearity and sensitivity across a broader spectrum of input values. It allows for a more comprehensive assessment of the sensor’s response, identifying potential non-linear characteristics.
- Least Squares Fitting: A mathematical approach that minimizes the difference between the sensor’s output and the expected output based on a set of calibration points. This method is particularly useful for sensors with non-linear responses, providing a precise representation of the sensor’s characteristic curve.
Importance of Proper Calibration
Proper calibration is essential for obtaining accurate and reliable measurements. Inaccurate calibration can lead to significant errors in calculated values, affecting downstream processes and potentially causing operational issues. For instance, in a manufacturing setting, an incorrectly calibrated sensor could lead to incorrect product dimensions, impacting quality control and potentially causing costly production errors.
Performance Testing Procedures for Compact Sensors
Rigorous testing procedures are crucial to assess the sensor’s performance characteristics. These procedures often involve evaluating parameters like sensitivity, resolution, response time, and stability.
- Sensitivity Testing: Measuring the sensor’s output in response to incremental changes in the input quantity. This helps determine the sensor’s sensitivity, ensuring it accurately detects small changes.
- Resolution Testing: Evaluating the smallest discernible change in the input quantity that results in a detectable change in the sensor’s output. This is crucial for applications demanding high precision.
- Response Time Testing: Measuring the time it takes for the sensor to reach a stable output after a change in the input quantity. This is critical for applications where fast response is essential, such as process control systems.
- Stability Testing: Assessing the sensor’s output over an extended period under stable environmental conditions. This ensures the sensor’s readings remain consistent over time.
Calibration Methods, Testing Equipment, and Expected Results
The following table summarizes various calibration and testing methods, along with associated equipment and anticipated outcomes.
Calibration Method | Testing Equipment | Expected Results |
---|---|---|
Standard Reference Sources | Calibrated weights, temperature baths, pressure gauges | Accurate measurements, traceable to national standards, demonstrating high reliability |
Multi-point Calibration | Calibration equipment, data acquisition system | Linearity and sensitivity data over a range of input values, identifying potential non-linear responses |
Least Squares Fitting | Data acquisition system, software for curve fitting | Precise representation of the sensor’s characteristic curve, minimizing error |
Sensitivity Testing | Controlled input source, data acquisition system | High sensitivity, accurately detecting small changes in the input |
Resolution Testing | Precision input control, data acquisition system | High resolution, detecting small changes in the input |
Integration and Interfacing
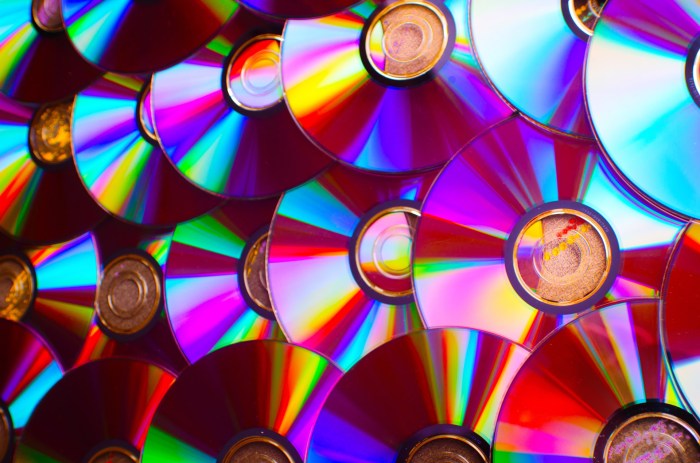
Compact sensors, often designed for miniaturization, must seamlessly integrate into larger systems. This integration necessitates careful consideration of communication protocols, connection methods, and control mechanisms to ensure reliable data transfer and efficient operation within the overall system architecture. The effective interfacing of compact sensors is crucial for their practical application.
Integration Methods
The integration of compact sensors into larger systems involves several key methods. These methods must account for the sensor’s physical size, power requirements, and the communication demands of the host system. Careful selection of integration methods is critical for efficient operation and minimal interference.
- Direct Wiring: For simple systems with minimal processing requirements, direct wiring can be a viable option. This approach involves physically connecting the sensor to the system’s circuitry using appropriate cables and connectors. This method is often cost-effective but may not be scalable for complex applications. Examples include temperature sensors connected to a simple data acquisition system.
- Embedded Systems: In many instances, compact sensors are integrated into dedicated embedded systems. These systems handle data acquisition, processing, and communication tasks, often including specialized hardware and software for optimized performance. This approach is well-suited for applications requiring real-time processing and control.
- Network Integration: In larger, distributed systems, sensors are frequently integrated through network communication protocols. This allows for centralized data collection and processing across various nodes. This method is often preferred for industrial automation and monitoring systems, where data from numerous sensors needs to be collected and analyzed.
Communication Protocols
The choice of communication protocol is critical for efficient and reliable data transfer. Various protocols cater to different needs, considering factors such as speed, distance, and data volume.
- SPI (Serial Peripheral Interface): SPI is a synchronous serial communication protocol suitable for short-range, high-speed data transfer. It’s commonly used in embedded systems, offering a simple and efficient way to communicate between devices. SPI is well-suited for applications requiring high throughput, such as image sensors or sensor arrays.
- I²C (Inter-Integrated Circuit): I²C is a multi-master, two-wire serial communication protocol widely used for sensor interfacing. Its simplicity and low power consumption make it a popular choice for integrating multiple sensors into a system. A prime example is in systems monitoring multiple environmental parameters like temperature, humidity, and light.
- UART (Universal Asynchronous Receiver/Transmitter): UART is a versatile asynchronous serial communication protocol. It’s a basic but reliable method for data transmission between sensors and controllers, suitable for applications with lower data rate requirements. A common example is in low-cost, simple data acquisition systems.
- CAN (Controller Area Network): CAN is a robust communication protocol used in automotive and industrial applications. It’s capable of handling high-speed data transfer and fault tolerance, making it ideal for distributed sensor networks. An instance is in vehicle diagnostics, where multiple sensors communicate critical data.
Interfacing Methods and Advantages
Different interfacing methods offer varying advantages, depending on the specific application requirements. This table summarizes common methods and their key benefits.
Interfacing Method | Advantages |
---|---|
Direct Wiring | Simple, cost-effective for small systems; high speed in short distances |
Embedded Systems | Real-time processing, optimized performance; dedicated hardware and software |
Network Integration | Centralized data collection; scalability for large systems; flexible data transfer |
SPI | High speed; simple implementation |
I²C | Low power; multi-master capability |
UART | Simple; cost-effective for lower data rate applications |
CAN | Robust communication; fault tolerance; high-speed data transfer |
Cost Considerations for Compact Sensors
The cost of compact sensors is a crucial factor in their adoption across diverse applications. Understanding the driving forces behind these costs is essential for optimizing design choices and selecting the most suitable sensor type for a given need. This section delves into the factors influencing cost, the relationship between performance and cost, and the trade-offs inherent in different sensor types.
Factors Influencing Compact Sensor Cost
Several key factors contribute to the overall cost of a compact sensor. Material costs, manufacturing processes, and design complexity are prominent elements. Sophisticated sensing mechanisms, advanced signal processing circuitry, and intricate packaging often elevate the cost. The scale of production also plays a critical role, as larger production runs typically lead to lower per-unit costs. Furthermore, regulatory compliance and testing requirements can add significant overhead, impacting the final price.
Relationship Between Performance and Cost
Generally, there is a direct correlation between sensor performance and cost. Higher performance parameters, such as accuracy, precision, and measurement range, frequently translate to more complex designs and higher-grade materials. This increase in sophistication naturally leads to a higher production cost. Consequently, selecting a sensor with the precise performance characteristics required for the application is critical to balancing cost and performance needs.
For instance, a sensor capable of measuring temperature with sub-degree precision might be significantly more expensive than a sensor designed for basic temperature monitoring.
Trade-offs Between Cost and Performance for Different Applications
The optimal balance between cost and performance varies significantly depending on the application. In industrial automation, where high reliability and repeatability are paramount, a higher cost sensor might be justified if it ensures continuous operation and reduces downtime. Conversely, in consumer electronics, where affordability is often a priority, lower-cost sensors with acceptable performance levels may suffice. Consider a smart thermostat: high precision in temperature measurement is not critical for comfort, whereas a high-precision accelerometer is essential for a navigation system in a car.
Comparison of Sensor Types
Sensor Type | Typical Cost (USD) | Accuracy (e.g., % error) | Typical Applications |
---|---|---|---|
Pressure Sensors (MEMS) | $0.50 – $5.00 | ±1% | Consumer electronics, automotive |
Accelerometers (MEMS) | $1.00 – $10.00 | ±0.1% | Mobile devices, industrial control |
Optical Sensors (Proximity) | $2.00 – $20.00 | ±0.5mm | Automated assembly lines, robotics |
Temperature Sensors (Thermistors) | $0.10 – $1.00 | ±1°C | HVAC systems, consumer appliances |
The table above presents a simplified comparison. Actual costs can vary significantly based on specific specifications, volume, and vendor. For instance, specialized pressure sensors used in aerospace applications can cost several hundred dollars or more. Similarly, the accuracy figures are representative and may vary based on the exact model and usage conditions.
Future Trends in Compact Sensors
Compact sensors are rapidly evolving, driven by the need for smaller, more powerful, and cost-effective sensing solutions. These advancements are fueling innovation across diverse sectors, from industrial automation to consumer electronics. This evolution is particularly notable in areas like miniaturization, integration, and enhanced performance capabilities.
Advancements in Miniaturization and Integration
Miniaturization is a key driver in the evolution of compact sensors. Continuing improvements in fabrication techniques allow for the creation of increasingly smaller sensors with comparable or even superior performance. Integration is another critical aspect, where multiple sensor functionalities are combined onto a single chip, leading to reduced size and increased efficiency. This integration trend is further enabled by advancements in microelectronics and nanotechnology, offering enhanced performance and lower power consumption.
Emerging Technologies and Applications
The landscape of compact sensor technology is continuously expanding with the emergence of new materials and techniques. This dynamic environment presents exciting possibilities for a wider range of applications.
Emerging Technology | Potential Applications |
---|---|
Microelectromechanical Systems (MEMS) | MEMS-based accelerometers, gyroscopes, and pressure sensors are crucial in automotive safety systems, smartphones, and industrial robotics. Further advancements are anticipated in higher sensitivity and lower power consumption. |
Nanomaterials (e.g., graphene, carbon nanotubes) | These materials offer exceptional sensitivity and conductivity, potentially revolutionizing sensors for chemical and biological detection. For example, graphene-based sensors could detect minute concentrations of pollutants in air or water. |
Optical Sensors | Optical sensors, particularly those employing fiber optics, are increasingly used for remote sensing, environmental monitoring, and medical diagnostics. These sensors are often advantageous for their non-contact measurement capability. |
Wireless Sensing | Wireless technologies enable data collection in challenging or remote locations. Examples include sensors for agricultural monitoring, structural health assessment, and environmental monitoring in harsh environments. Low-power, long-range wireless communication protocols are a key element in these advancements. |
Artificial Intelligence (AI) Integration | AI algorithms can be integrated into compact sensors to enhance data processing and interpretation. This allows for real-time analysis and predictive capabilities, which can be applied in various domains, including medical diagnostics and industrial automation. |
Potential Impact on Various Industries
The advancements in compact sensors will significantly impact numerous industries. For example, in the automotive industry, enhanced safety features and autonomous driving capabilities will rely on sophisticated sensor systems. In healthcare, compact sensors will lead to improved diagnostics and monitoring devices, potentially enabling remote patient care. Furthermore, the agricultural sector will benefit from precision farming technologies facilitated by compact sensors for environmental monitoring and crop management.
Case Studies of Compact Sensor Applications
Compact sensors are increasingly prevalent in diverse applications, offering significant advantages in terms of size, cost, and power consumption. This section presents real-world case studies to illustrate the practical implementation and benefits of these technologies. From industrial automation to consumer electronics, compact sensors are transforming how we interact with and monitor the world around us.
Industrial Automation
Compact sensors are revolutionizing industrial automation by enabling smaller, more efficient, and cost-effective solutions. Their integration into machinery allows for real-time monitoring and control, leading to increased productivity and reduced downtime.
- Automated Assembly Line: A manufacturer of electronic components uses compact proximity sensors to monitor the positioning of parts during assembly. These sensors, significantly smaller than traditional options, enable precise placement, preventing errors and improving throughput. The reduced size allows for placement in tight spaces, previously inaccessible to larger sensors. This leads to improved assembly efficiency, and reduced errors, saving time and resources.
- Robotics in Warehousing: Compact optical sensors are utilized in robotic systems for warehouse automation. These sensors precisely detect and identify objects, enabling robots to navigate and pick items accurately. This application demonstrates how compact sensors can enhance the efficiency of complex robotic systems in large-scale environments.
Consumer Electronics
Compact sensors are transforming consumer electronics by enabling sophisticated features in smaller form factors.
- Smartphones and Wearables: Accelerometers and gyroscopes in smartphones and fitness trackers are prime examples of compact sensors. These sensors provide accurate motion data for applications like gaming, navigation, and activity tracking. The miniature design allows for integration into increasingly slim and portable devices.
- Automotive Applications: Compact sensors play a critical role in advanced driver-assistance systems (ADAS). Their small size enables the integration of multiple sensors into dashboards and cockpits, offering enhanced safety features like lane departure warnings and adaptive cruise control. This demonstrates the importance of size reduction in critical safety systems.
Medical Devices
Compact sensors are finding applications in medical devices for monitoring vital signs and providing real-time feedback.
- Portable Blood Pressure Monitors: Compact pressure sensors in portable blood pressure monitors provide accurate readings in a user-friendly format. The compact design makes the device more portable and convenient for patients and healthcare professionals.
- Implantable Sensors: Miniaturized sensors are being developed for use in implantable medical devices. These sensors continuously monitor various physiological parameters, allowing for early detection of health issues and improved patient care. This illustrates the future potential of compact sensors in medical diagnostics.
Table of Case Studies
Case Study | Application | Key Outcomes |
---|---|---|
Automated Assembly Line | Industrial Automation | Improved accuracy, increased throughput, reduced errors |
Robotics in Warehousing | Industrial Automation | Enhanced navigation and object recognition |
Smartphones and Wearables | Consumer Electronics | Accurate motion data for various applications |
Automotive Applications | Consumer Electronics | Improved safety features in ADAS |
Portable Blood Pressure Monitors | Medical Devices | Accurate and convenient blood pressure monitoring |
Implantable Sensors | Medical Devices | Continuous physiological monitoring and early detection |
End of Discussion
In conclusion, compact sensors have revolutionized various sectors by offering a powerful blend of functionality and portability. Their continued evolution promises even more innovative applications in the future. We’ve explored the key components of these remarkable devices, highlighting their potential across diverse fields.
Commonly Asked Questions
What are the typical size ranges for compact sensors?
Typical size ranges vary significantly depending on the specific sensor type and application. However, compact sensors generally aim for miniaturization while maintaining essential performance characteristics. Precise size details are often found within product specifications.
How do compact sensors compare in cost to larger sensors?
Compact sensors often have a higher cost per unit than larger sensors, owing to the complex design and fabrication processes. However, the benefits of miniaturization, such as improved portability and integration, can offset these costs for many applications.
What are the common communication protocols used for compact sensors?
Common communication protocols for compact sensors include I2C, SPI, and UART, each with its own strengths and weaknesses in terms of speed, complexity, and power consumption. The selection depends on the application’s specific requirements.