Circuit board review is a crucial process in the electronics industry. It ensures the quality and functionality of circuit boards, identifying potential issues before they impact the final product. This guide provides a detailed overview of the entire review process, from initial inspection to final reporting.
Thorough circuit board reviews are essential for various applications, from consumer electronics to industrial machinery. Understanding the methods, techniques, and potential pitfalls is key to maintaining high standards and avoiding costly errors.
Introduction to Circuit Board Reviews
A circuit board review is a systematic examination of a printed circuit board (PCB) to identify potential design flaws, manufacturing defects, and functional issues. This process is crucial for ensuring the quality, reliability, and safety of electronic devices. A thorough review can uncover errors early in the design or manufacturing process, preventing costly rework or failures later on.Circuit board reviews are critical in various applications, from consumer electronics to industrial control systems.
Their importance lies in the potential for significant cost savings, improved product quality, and enhanced safety. A properly executed review process can significantly reduce the likelihood of product recalls and customer dissatisfaction.
Circuit Board Review Process Steps
A typical circuit board review involves a multi-step process, focusing on different aspects of the board. Understanding each step is essential for a comprehensive evaluation. These steps are designed to cover all potential issues from design to testing.
- Design Review: This phase examines the schematic diagrams, component placement, and signal routing to identify design errors, potential conflicts, and adherence to design rules. Identifying design flaws early in the process avoids significant rework later on.
- Manufacturing Review: This step involves examining the physical board for manufacturing defects, such as component misplacement, solder bridging, or incorrect component values. A review of the manufacturing process ensures the board meets the design specifications and the quality standards.
- Testing Review: This involves evaluating the board’s functionality through various testing procedures. It examines the board’s performance under different operating conditions, including voltage, temperature, and load. Identifying any deviations from expected performance is crucial to correcting issues before the product is released.
Types of Circuit Board Reviews
Different types of circuit board reviews cater to specific needs and applications. Each type emphasizes different aspects of the board.
- Design Reviews: Focuses on the schematic, layout, and component selection. These reviews help identify design flaws, potential issues, and ensure adherence to design standards. A thorough design review helps to avoid costly rework in later stages of production.
- Manufacturing Reviews: Assess the manufacturing process and the physical PCB. It ensures the board meets the required specifications and detects manufacturing defects like wrong component placements, solder issues, and quality control deficiencies. This process is crucial for maintaining product quality and consistency.
- Testing Reviews: Evaluate the board’s functionality through testing procedures. These reviews identify discrepancies in performance, reliability, and safety under different conditions. This phase aims to guarantee that the board operates as expected in its intended application.
Review Methods and Techniques
Circuit board reviews are crucial for ensuring functionality, reliability, and safety. Proper review methods and techniques are essential to identify potential defects, design flaws, and compliance issues early in the manufacturing process. This section details various methods for inspecting circuit boards and the testing procedures involved, offering a comparative analysis of different inspection tools and techniques.Different inspection methods and tools are employed depending on the complexity of the circuit board and the specific requirements of the project.
Understanding the strengths and weaknesses of each method is essential for making informed decisions regarding the review process. Accurate identification and resolution of defects contribute significantly to the overall success of the product.
Inspection Methods for Circuit Boards
Various methods are utilized for inspecting circuit boards, each with its own strengths and limitations. Visual inspection, a fundamental method, is often the initial step in identifying gross defects like missing components, solder bridges, or bent pins.
- Visual Inspection: This method relies on the examiner’s keen eye to spot defects like missing components, solder bridges, or bent pins. Magnification tools, such as magnifying glasses or microscopes, are frequently employed to enhance the visibility of fine details.
- X-ray Inspection: X-ray inspection is valuable in revealing internal component placement and identifying potential short circuits or hidden defects, particularly useful for inspecting multilayer boards.
- Electrical Testing: Electrical testing is crucial to verify the functionality of individual components and the continuity of circuits. This can include resistance measurements, voltage checks, and current measurements. Specific test equipment like multimeters and oscilloscopes are used for these tests.
- Automated Optical Inspection (AOI): AOI systems utilize cameras and sophisticated image processing to detect defects in circuit boards automatically. This method is highly effective in finding subtle defects that might be missed during visual inspection.
Testing Procedures for Circuit Board Reviews
Effective testing procedures are vital to validate the functionality and integrity of circuit boards. These procedures typically involve a systematic approach to check for potential failures and deviations from design specifications.
- Functional Testing: This procedure assesses the overall functionality of the circuit board under various operating conditions, confirming that the circuit board performs according to its design specifications. Test cases, often derived from the circuit board’s intended application, are used to validate functionality.
- Environmental Testing: Circuit boards are often subjected to various environmental stresses, such as temperature extremes, humidity, and vibration, to ensure they function reliably under expected conditions. These tests help in identifying potential failures due to environmental factors.
- Fault Isolation Testing: This procedure involves isolating and identifying the exact location of a fault or defect on the circuit board. This can involve pinpointing specific components or circuit paths that are malfunctioning.
Comparison of Inspection Tools and Techniques
Different inspection tools and techniques offer varying levels of accuracy and efficiency. Choosing the right method depends on the specific requirements of the project.
Inspection Method | Pros | Cons |
---|---|---|
Visual Inspection | Cost-effective, readily available tools | Limited resolution, susceptible to human error |
X-ray Inspection | Identifies internal defects, high resolution | Can be expensive, requires specialized equipment and expertise |
Electrical Testing | Precise identification of electrical faults, high accuracy | Can be time-consuming, requires specific equipment and expertise |
AOI | High throughput, automated, reduces human error | Can miss complex defects, requires sophisticated equipment and setup |
Identifying Defects and Issues
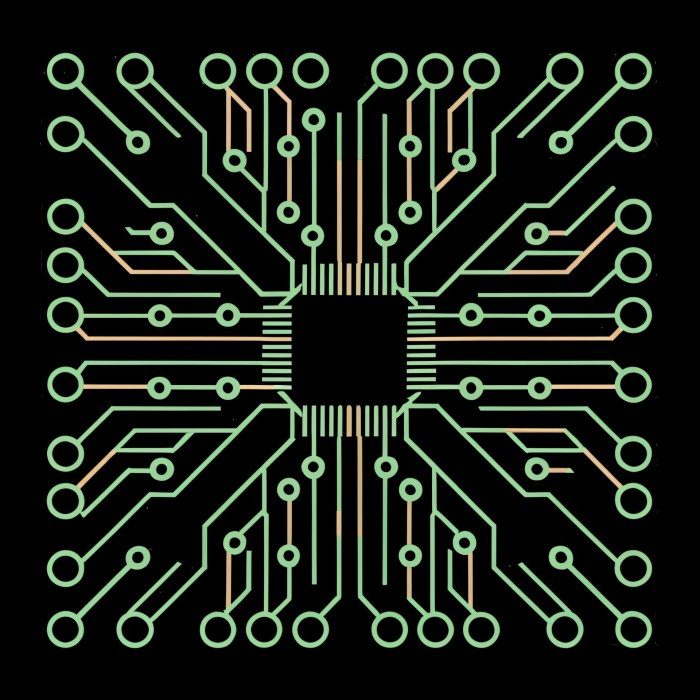
Pinpointing flaws in circuit boards is crucial for ensuring functionality, reliability, and safety. A meticulous review process helps to detect and classify these issues, leading to effective troubleshooting and resolution. This section delves into common defects, providing examples and a structured approach to identification.Identifying and classifying defects during circuit board reviews is a critical step in the overall quality assurance process.
Early detection of flaws often translates to lower repair costs and quicker time-to-market. The proper categorization of defects also facilitates targeted corrective actions, ultimately enhancing the quality and reliability of the final product.
Common Defects
A thorough review often uncovers a range of defects, from minor cosmetic issues to severe structural problems. Understanding these common types helps expedite the identification and resolution process.
- Solder Defects: These are prevalent issues, including insufficient solder joints, cold solder joints, and solder bridging. Insufficient solder joints may lead to weak connections, while cold solder joints can result in intermittent failures. Solder bridging occurs when solder connects two or more components that shouldn’t be electrically connected, potentially leading to short circuits.
- Component Placement Errors: Incorrect component placement can lead to a wide range of issues. This includes components placed in the wrong orientation or at the wrong location on the board. Misplaced components can cause functional problems, ranging from minor performance degradation to complete circuit failure.
- Short Circuits: Short circuits, where two or more conductive paths connect unexpectedly, are a significant concern. They can result from solder bridging, damaged insulation, or improper component placement. Short circuits often lead to excessive current flow, potentially damaging components and the board itself.
- Open Circuits: Open circuits occur when a conductive path is interrupted. This can result from component failures, breaks in traces, or improper connections. Open circuits can lead to a lack of signal transmission, rendering the circuit non-functional.
- Incorrect Component Value: Using the wrong component value can lead to malfunctions in the circuit’s operation. For example, using a resistor with the incorrect resistance value can cause an incorrect current flow or voltage drop, disrupting the intended circuit functionality.
Defect Severity and Impact
Categorizing defects based on their severity and impact facilitates prioritization and resource allocation. This classification allows for a structured approach to addressing defects and mitigating risks.
Defect Category | Severity Level | Impact | Action Required |
---|---|---|---|
Minor Solder Defects (e.g., small voids) | Low | Potential for intermittent failure | Repair or rework as needed |
Component Placement Errors | Medium | Functional impairment, potential for circuit failure | Component replacement or repositioning |
Short Circuits | High | Immediate damage to components, possible fire hazard | Isolate and repair the faulty circuit section immediately |
Open Circuits | High | Complete circuit failure | Identify and repair the open circuit |
Incorrect Component Value | Medium | Functional impairment, potential for circuit failure | Replace the component with the correct value |
Identifying and Classifying Defects
Utilizing appropriate tools and techniques is essential for accurate defect identification and classification. Visual inspection, combined with appropriate test equipment, ensures comprehensive defect detection.
- Visual Inspection: A visual inspection, using magnification if necessary, is the first step in identifying defects. Magnifying glasses, microscopes, and high-resolution cameras can aid in detecting minute solder defects, misaligned components, or trace breaks.
- Electrical Testing: Employing appropriate electrical testing equipment, such as multimeters and oscilloscopes, is crucial for identifying short circuits, open circuits, and incorrect component values. This helps determine if a circuit is functioning as intended.
- Automated Optical Inspection (AOI): Automated Optical Inspection systems can rapidly scan circuit boards, identifying a wide range of defects. AOI systems are particularly useful for high-volume production, enhancing defect detection efficiency.
Documentation and Reporting
Accurate documentation is crucial in circuit board reviews. Detailed records ensure reproducibility of the review process, facilitate communication among team members, and support future troubleshooting or modifications. Thorough documentation helps track the progress of the review and provides a permanent record of findings, ensuring accountability and traceability.
Importance of Accurate Documentation
Proper documentation in circuit board reviews minimizes ambiguity and ensures a clear understanding of the review’s findings. This detailed record is vital for identifying trends, patterns, and potential systemic issues in the manufacturing process or design. A well-documented review allows for the effective communication of issues to the relevant stakeholders and facilitates the implementation of corrective actions. It’s a key element for continuous improvement in the production process.
Format and Content of a Comprehensive Review Report
A comprehensive review report should be structured logically and contain all essential information. It should include a clear introduction outlining the scope of the review, the methodology employed, and the objective of the review. Detailed descriptions of the defects or issues encountered, along with their location on the circuit board, are critical. The report should present supporting evidence, such as photographs or diagrams, to corroborate the findings.
Recommendations for corrective actions, based on the identified defects, should be clearly articulated, along with any associated timelines.
Template for Documenting Findings
A standardized template for documenting findings during a circuit board review streamlines the process and ensures consistency. The template should include fields for the date of the review, the reviewer’s name, the circuit board identification number, and the specific components or areas examined. Crucially, it should have dedicated sections for documenting the type of defect (e.g., solder bridging, component misalignment), the severity of the defect, and the location of the defect on the board (using coordinates or a clear description).
The template should also allow for notes, observations, and supporting evidence to be recorded.
A quick circuit board review reveals potential compatibility issues, especially concerning power delivery. Considering the advancements in battery technology, like those explored in battery 2025 , further testing is needed to ensure optimal performance. A more detailed analysis of the circuit board’s power management system is crucial for future iterations.
Date | Reviewer | Circuit Board ID | Component/Area | Defect Type | Severity | Location | Notes/Observations | Supporting Evidence |
---|---|---|---|---|---|---|---|---|
2024-10-27 | John Smith | CB-1234 | IC Socket J1 | Component Misalignment | High | X: 2.5cm, Y: 1.8cm | Component slightly displaced from intended location. | Photograph of the defect |
Examples of Different Types of Review Reports
Review reports can vary in format depending on the specific needs and requirements of the review. One common type is a detailed report that meticulously documents every identified defect. A summary report, on the other hand, provides a concise overview of the key findings, highlighting the most significant issues. A report focused on specific manufacturing processes might pinpoint deviations from standard operating procedures, offering detailed insights into areas needing improvement.
An executive summary report, geared towards high-level stakeholders, provides a high-level overview of the findings and the recommended corrective actions.
Tools and Technologies: Circuit Board Review
Effective circuit board reviews rely heavily on a diverse array of tools and technologies, from specialized instruments to sophisticated software applications. These tools enable a thorough examination of the board’s design, construction, and functionality, facilitating the identification and resolution of potential issues. Employing these tools efficiently is crucial for ensuring product quality and reliability.
Specialized Tools
A range of specialized tools facilitates detailed inspection and analysis of circuit boards. These tools provide precise measurements and visual aids for identifying anomalies. Microscopes, for instance, are invaluable for examining fine-line features, component placement, and trace continuity. Specialized probes enable precise measurements of voltage, current, and resistance in specific points on the board. These instruments are essential for pinpointing the source of errors and ensuring that the circuit operates as intended.
Electronic Test Equipment
A wide array of electronic test equipment is crucial for evaluating the functionality of circuit boards. These instruments can be broadly classified into several categories. Oscilloscopes, for instance, are used to visualize electrical waveforms, helping to identify signal distortions or timing issues. Multimeters, indispensable for measuring voltage, current, and resistance, provide basic but essential checks on the circuit’s operational parameters.
Logic analyzers, on the other hand, capture and analyze digital signals, which are vital for verifying the proper functioning of digital circuits. These instruments aid in identifying errors and inconsistencies in the board’s design and construction.
Software Tools
Software tools play a pivotal role in circuit board analysis. These tools assist with schematic capture, simulation, and analysis, streamlining the review process. Computer-aided design (CAD) software is commonly used to generate accurate representations of the circuit board layout, facilitating visual inspections and the detection of potential design flaws. Simulation software allows for testing circuit functionality before physical prototypes are built, significantly reducing development time and costs.
Such tools are crucial for identifying and rectifying design errors at an early stage.
Automation
Automation plays a significant role in streamlining circuit board review processes. Automated testing systems can perform repetitive tasks, such as component verification and signal integrity checks, freeing up reviewers to focus on complex issues and critical areas. These automated systems provide comprehensive data analysis, identify potential problems more quickly, and enhance the accuracy of reviews. Machine learning algorithms can also be integrated into automated systems, allowing them to identify anomalies and patterns that might be missed by human reviewers.
This capability can dramatically improve the efficiency and effectiveness of circuit board reviews.
Design Considerations for Review
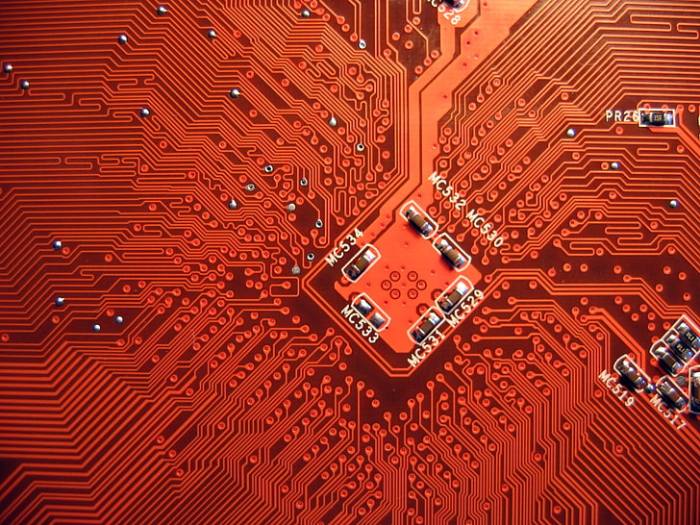
Effective circuit board reviews hinge significantly on the quality and clarity of the design itself. Poorly conceived designs can lead to extended review times, increased error rates, and ultimately, a compromised product. Understanding the critical design considerations is paramount for streamlining the review process and ensuring a high-quality outcome.A well-structured design facilitates a thorough review, allowing reviewers to readily identify potential issues.
Conversely, a poorly organized design can hinder the review process, leading to confusion and missed defects. Proactive consideration of these design elements is crucial for efficient and comprehensive reviews.
Design Layout and Component Placement
Careful consideration of component placement and overall layout significantly impacts review efficiency. Clear and logical arrangement promotes easy identification of signal paths, power distribution, and potential interference points. Complicated or cramped layouts can lead to ambiguities in the circuit’s operation, making it difficult to understand the intended function and identify potential issues. This often results in extended review times and an increased risk of overlooking crucial details.
Signal Integrity and Routing
Appropriate signal routing and consideration of signal integrity are critical for avoiding signal degradation and noise issues. Overcrowded routing channels or inadequate spacing between components can lead to signal reflections, crosstalk, and other undesirable effects. Poor signal integrity can cause intermittent malfunctions and make the circuit difficult to diagnose during the review process. This can significantly impact the review efficiency and overall product reliability.
Power Distribution and Grounding
Effective power distribution and grounding are essential for stable circuit operation. Insufficient or improperly designed power planes can lead to voltage fluctuations and noise, impacting component performance. Inadequate grounding can lead to short circuits, which can cause malfunctions and even damage during the review process. A clear and well-defined power distribution and grounding scheme is paramount for reliable circuit operation and a smooth review.
Documentation and Standards Adherence
Adherence to established design standards and comprehensive documentation are crucial. Clear documentation helps reviewers quickly understand the design intent and expected behavior. Lack of proper documentation can result in ambiguity, requiring significant effort to clarify design details, hindering review efficiency and potentially increasing the risk of errors. Using consistent and well-defined design standards facilitates the review process, as it reduces the need for extensive clarification.
Table of Best Practices for Circuit Board Design for Review
Design Consideration | Best Practice | Impact on Review |
---|---|---|
Layout | Logical and organized arrangement of components, with clear signal paths and ample spacing. | Reduces review time and increases accuracy. |
Signal Integrity | Optimized routing, sufficient spacing between components, and consideration of signal reflections and crosstalk. | Ensures stable signal transmission, reducing the risk of intermittent errors. |
Power Distribution | Clear and well-defined power planes, appropriate decoupling capacitors, and proper grounding schemes. | Ensures stable voltage and reduces noise, facilitating accurate reviews. |
Documentation | Comprehensive documentation including schematics, bill of materials, and design specifications. | Allows reviewers to quickly understand the design intent, improving efficiency and accuracy. |
Troubleshooting and Problem Solving
Troubleshooting circuit boards effectively involves a systematic approach to identify and rectify issues. A well-defined process, coupled with a thorough understanding of circuit diagrams and potential problem areas, is crucial for successful repair and maintenance. This section details the steps and strategies for diagnosing and resolving problems encountered during a circuit board review.
A quick circuit board review often needs a deep dive into specific components. One crucial area is RAM, and the RAM 2025 specs ( RAM 2025 ) offer a fascinating look at potential future improvements. Ultimately, a comprehensive circuit board review needs to consider these cutting-edge developments.
Systematic Troubleshooting Process
A systematic approach to troubleshooting is essential to efficiently pinpoint the root cause of a problem. This process typically involves several stages, progressing from general observations to specific component analysis. A logical sequence ensures that no potential cause is overlooked.
- Initial Assessment: Begin by carefully examining the circuit board for any visible defects, such as burnt components, missing parts, or unusual discoloration. This initial visual inspection often reveals the nature of the problem and guides subsequent investigation.
- Data Collection: Gather all available data related to the circuit board’s performance. This includes the circuit’s specifications, schematics, operational parameters, and any relevant test results. Accurate data collection provides a comprehensive understanding of the expected behavior of the circuit.
- Hypothesis Formulation: Based on the initial assessment and data collected, formulate potential hypotheses regarding the source of the problem. Consider known failures, design flaws, and environmental factors. This stage requires critical thinking and an understanding of the circuit’s function.
- Testing and Verification: Conduct targeted tests to verify the validity of each hypothesis. Use appropriate test equipment to measure voltage, current, resistance, and other relevant parameters. This process involves checking individual components and their interconnections.
- Root Cause Analysis: Once the problem is identified, determine the underlying cause. This step involves examining the design, manufacturing process, and operating conditions to pinpoint the source of the issue. This often requires tracing the signal paths on the circuit board and checking component specifications.
- Solution Implementation: Develop and implement a solution to address the root cause of the problem. This may involve replacing faulty components, adjusting settings, or modifying the circuit design. Implementing a solution requires careful consideration and adherence to safety procedures.
- Verification and Documentation: Verify that the implemented solution has resolved the problem. Document the troubleshooting process, including the steps taken, observations made, and the solution implemented. This ensures repeatability and allows for future reference.
Identifying Root Causes, Circuit board review
Determining the root cause is critical for preventing future issues. A thorough analysis considers the potential contributing factors, such as design flaws, manufacturing defects, environmental conditions, and operational errors.
- Design Flaws: A poorly designed circuit can lead to various problems. Consider the component tolerances, signal integrity, and thermal dissipation. Verify component ratings, power dissipation limits, and thermal resistance.
- Manufacturing Defects: Defective components or incorrect connections during assembly can introduce faults. Inspect the soldering quality, component placement, and any physical damage to the board. Examine component specifications for appropriate values and tolerances.
- Environmental Factors: Exposure to extreme temperatures, humidity, or electromagnetic interference can damage components and lead to malfunctions. Consider the operating environment and its impact on the circuit board.
- Operational Errors: Incorrect use or improper operation can lead to damage or malfunctions. Review operational procedures and ensure proper handling of the circuit board.
Using Circuit Diagrams
Circuit diagrams provide a visual representation of the circuit’s components and connections. Analyzing the diagram helps to pinpoint the problematic area and understand the signal flow.
- Component Identification: Identify the components involved in the circuit and their corresponding locations on the board using the circuit diagram. This is vital for accurate diagnosis and troubleshooting.
- Signal Tracing: Trace the signal paths on the circuit diagram to understand how the signals travel through the circuit. Identify any potential points of failure or interference along the signal path. Pay close attention to voltage drops, current flows, and signal integrity.
- Identifying Potential Fault Points: By understanding the circuit’s functionality, identify potential fault points on the diagram. Focus on components that are critical to the circuit’s operation. Consider the expected behavior of the circuit under normal conditions and deviations from these expectations.
Common Problems and Solutions
Some common problems encountered during circuit board reviews and their typical solutions are detailed below:
Problem | Solution |
---|---|
Open circuit | Verify component connections and repair or replace damaged components. |
Short circuit | Identify and remove the short circuit. This may involve replacing components or correcting wiring issues. |
Incorrect component value | Replace the component with the correct value. |
Component overheating | Increase cooling or reduce power consumption. Consider changing components to improve heat dissipation. |
Standards and Guidelines
Adherence to industry standards is critical for ensuring the quality, reliability, and safety of circuit boards. These standards encompass design specifications, manufacturing processes, and testing procedures, ultimately impacting the performance and longevity of the final product. Without standardized guidelines, inconsistencies and potential failures can arise during design, production, or even in the field.Following established standards promotes interoperability, reduces errors, and facilitates collaboration among different stakeholders in the electronics industry.
This allows for more efficient and effective circuit board reviews, as everyone is working within a shared framework of expectations.
Key Industry Standards
Various organizations develop and maintain standards relevant to circuit board design and manufacturing. These standards cover a wide range of aspects, from component specifications to environmental considerations. Understanding and applying these standards is crucial for effective circuit board reviews.
- IPC Standards: The Institute for Printed Circuit Boards (IPC) is a prominent organization that sets numerous standards for printed circuit board (PCB) design, fabrication, assembly, and testing. These standards encompass a comprehensive set of guidelines for material selection, soldering processes, component placement, and electrical testing. The IPC-2221 standard, for instance, Artikels specific guidelines for surface mount technology (SMT) assembly.
Adherence to these standards ensures consistency in quality and reduces the likelihood of manufacturing defects.
- MIL-STD Standards: The Department of Defense (DoD) establishes standards (MIL-STD) for military applications. These standards focus on reliability, durability, and environmental robustness, often exceeding commercial standards in their stringent requirements. For instance, MIL-STD-883 defines various test methods for electronic components and assemblies. Reviews conducted for military applications require meticulous adherence to these standards to ensure the circuit board meets stringent performance and reliability criteria.
- IEC Standards: The International Electrotechnical Commission (IEC) develops international standards for electrical and electronic equipment. These standards address safety, electromagnetic compatibility (EMC), and environmental considerations. Compliance with IEC standards ensures that the circuit board meets international safety and EMC requirements. This is crucial for global market access.
- JEDEC Standards: The Joint Electron Device Engineering Council (JEDEC) establishes standards for semiconductor components, packages, and interfaces. These standards ensure compatibility and interchangeability between different semiconductor devices, impacting the design and integration of components on a circuit board. JEDEC standards influence the review process by dictating component selection and compatibility.
Impact on Review Process
Standards significantly influence the circuit board review process. They act as a benchmark for evaluating design and manufacturing adherence, ensuring that components and processes align with industry best practices.
Standard | Significance in Review |
---|---|
IPC Standards | Provides a structured framework for evaluating component placement, soldering quality, and overall manufacturing processes. Reviewers can use IPC standards to identify deviations from accepted practices and assess potential risks. |
MIL-STD Standards | Establishes rigorous requirements for reliability, environmental robustness, and durability, which are crucial for military and aerospace applications. Reviews need to verify the design and manufacturing meet these specific standards. |
IEC Standards | Ensures that the circuit board meets international safety and EMC regulations, allowing for broader market applicability. The review process should identify compliance with these international standards. |
JEDEC Standards | Crucial for verifying component compatibility and ensuring proper integration into the circuit board design. Review steps should verify the selection and use of components adheres to JEDEC standards. |
Example of Standard Impact
Consider a review of a circuit board designed for a medical device. The review team needs to confirm compliance with IEC standards for medical equipment, ensuring the board meets safety requirements for patient use. This might involve verifying insulation thicknesses, grounding procedures, and electromagnetic interference shielding, all Artikeld in IEC standards.
Advanced Circuit Board Review Topics
Circuit board reviews are evolving alongside the rapid advancements in electronic technology. Modern boards are increasingly complex, featuring high-density components and intricate designs. This necessitates the adaptation of review methodologies to effectively identify potential issues and ensure the quality and reliability of these sophisticated systems.
Emerging Technologies and their Impact
Emerging technologies, such as advanced packaging techniques and the integration of heterogeneous materials, significantly impact circuit board reviews. These innovations introduce new challenges in terms of inspection and analysis. For instance, the miniaturization of components makes traditional visual inspection methods less effective, demanding the implementation of more sophisticated techniques.
Advanced Techniques for High-Density Boards
High-density circuit boards present unique challenges for inspection. The close proximity of components and the intricate routing of traces necessitate specialized techniques to uncover hidden defects. Advanced imaging technologies, like high-resolution optical microscopy and advanced x-ray imaging, can penetrate these dense structures to reveal potential problems.
New Methods for Complex Designs
Inspecting complex circuit board designs, featuring multiple layers and intricate interconnections, requires innovative methodologies. Computer-aided design (CAD) data and simulations are increasingly utilized to identify potential design flaws before physical prototyping. Furthermore, the use of automated optical inspection systems allows for comprehensive analysis of large areas of the board, which are often impractical to examine manually.
Future Trends in Circuit Board Review
Future trends will shape circuit board review processes, focusing on automation, integration, and predictive analysis. The integration of machine learning algorithms into inspection systems will enable the identification of subtle defects that might be missed by human reviewers. Moreover, predictive modeling techniques will analyze historical data to forecast potential failures, allowing for proactive measures to be taken.
Final Thoughts
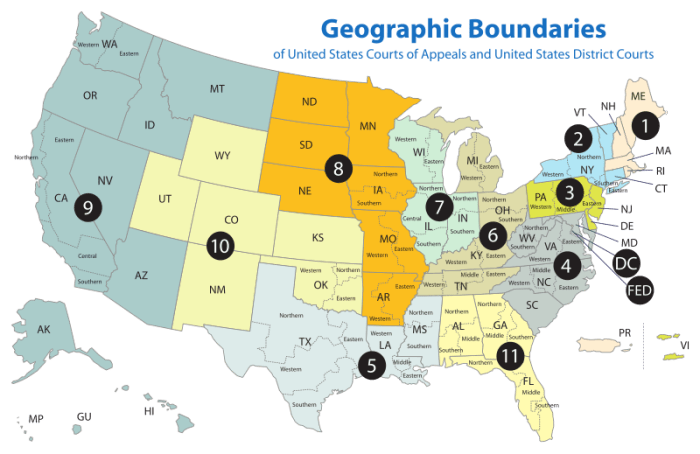
In conclusion, a comprehensive circuit board review involves meticulous inspection, defect identification, and accurate documentation. By following the Artikeld methods, techniques, and best practices, professionals can ensure the quality and reliability of circuit boards. The importance of adherence to industry standards and continuous improvement cannot be overstated. This comprehensive guide equips readers with the knowledge to confidently navigate the intricacies of circuit board reviews.
Common Queries
What are some common circuit board defects?
Common defects include solder bridging, component placement errors, short circuits, and open circuits. The severity and impact of these defects vary significantly.
What software tools aid in circuit board analysis?
Specialized software tools, often integrated with design tools, assist in simulating circuit behavior, identifying potential issues, and analyzing the impact of design changes. Some tools provide interactive simulations to visualize the behavior of circuits.
How do industry standards impact the review process?
Adherence to industry standards ensures consistency, reliability, and safety. These standards provide guidelines for design, manufacturing, and testing, which are crucial for ensuring the final product meets safety and performance expectations.
What are the steps involved in a typical circuit board review process?
Typical steps include visual inspection, functional testing, component verification, and detailed documentation. The specific steps may vary depending on the complexity of the circuit board and the review’s purpose.