Durable battery technology is rapidly evolving, pushing the boundaries of what’s possible in energy storage. This comprehensive guide delves into the intricacies of durable batteries, exploring their defining characteristics, performance metrics, and the various factors that influence their lifespan and reliability.
From the materials used in their construction to the environmental conditions they face, we’ll examine the entire lifecycle of a durable battery. This analysis will cover everything from basic definitions to advanced manufacturing techniques and future trends.
Defining Durable Battery
A durable battery is more than just a source of power; it’s a reliable component that consistently delivers expected performance throughout its lifespan. Durability encompasses various aspects, including extended operational life, resilience to stress, and resistance to physical damage. Understanding these characteristics is crucial for selecting the right battery for specific applications.This definition extends beyond simple capacity to include the battery’s ability to withstand environmental factors, physical shocks, and repeated charge/discharge cycles.
The longevity and consistent performance under demanding conditions are key indicators of a battery’s overall durability.
Factors Contributing to Battery Durability
Several key factors influence a battery’s durability. These include the materials used in its construction, the manufacturing process, and the design considerations for its internal components. Proper material selection plays a critical role in mitigating degradation during extended use.
- Material Composition: The chemical composition of the battery’s electrodes, electrolytes, and casing directly impacts its resistance to degradation and damage. Advanced materials often exhibit enhanced stability and resistance to corrosion, leading to longer lifespan.
- Manufacturing Process: Precise control over the manufacturing process, including material mixing, cell assembly, and quality control, is essential for consistent performance and reduced defects.
- Design Considerations: Battery design, such as cell configuration and internal structure, influences its resistance to physical stress. Robust packaging and protective coatings can shield the battery from external impacts.
- Environmental Factors: Exposure to extreme temperatures, humidity, and vibrations can accelerate battery degradation. Proper battery enclosures and designs are crucial for ensuring longevity in various operating environments.
Battery Types and Durability
Various battery chemistries exhibit different durability characteristics. The selection of the appropriate battery type depends on the specific application and its demands.
- Lithium-ion (Li-ion) Batteries: Li-ion batteries are widely used due to their high energy density and relatively long lifespan. They typically show excellent performance under stress and are resilient to physical damage, although specific Li-ion chemistries have different durability characteristics. Their lifespan can vary significantly based on factors such as charging and discharging patterns, temperature, and quality control during manufacturing.
Examples include LiFePO4 (lithium iron phosphate) and NMC (nickel-manganese-cobalt) batteries, each exhibiting different durability profiles.
- Alkaline Batteries: Alkaline batteries, while not as energy-dense as Li-ion, are known for their affordability and reliability in basic applications. Their durability is generally good for their intended use, but they have a shorter lifespan compared to Li-ion under heavy use or extreme conditions. They are commonly found in portable electronics, flashlights, and remote controls.
- Nickel-Cadmium (NiCd) Batteries: NiCd batteries, once widely used, have limitations in terms of durability. They suffer from the “memory effect” (where their capacity diminishes after repeated partial discharges) and have a relatively shorter lifespan compared to Li-ion or newer technologies. Their use is now less common due to environmental concerns related to cadmium.
Durability Comparison Table
Battery Type | Energy Density | Lifespan | Performance Under Stress | Resistance to Damage | Cost |
---|---|---|---|---|---|
Lithium-ion (Li-ion) | High | Generally Long | Excellent | Good | Moderate to High |
Alkaline | Moderate | Moderate | Good | Fair | Low |
Nickel-Cadmium (NiCd) | Moderate | Short | Fair | Fair | Low |
Performance Metrics
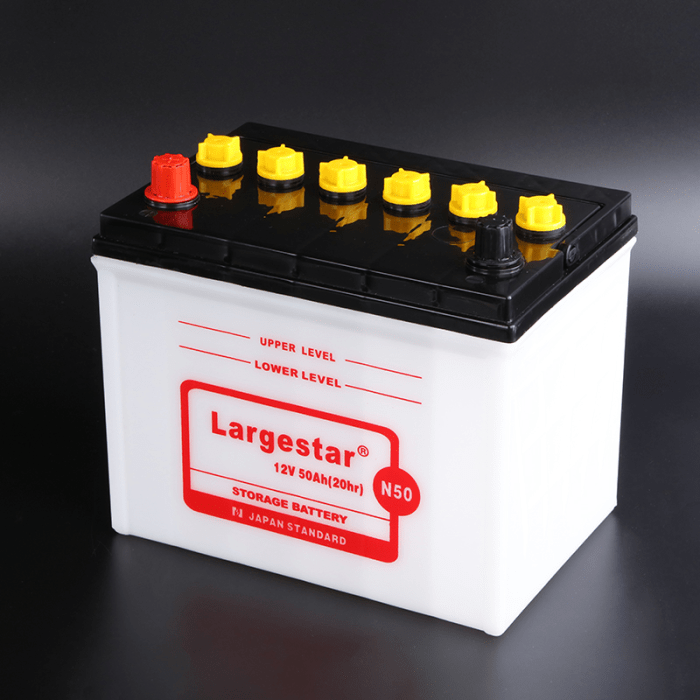
Battery durability is crucial for various applications, from portable electronics to electric vehicles. Understanding how batteries perform over time is essential for predicting their lifespan and reliability. This section details the key performance metrics used to evaluate battery durability, along with their measurement and interpretation.Battery performance metrics are used to assess the ability of a battery to retain its capacity and function reliably throughout its lifespan.
These metrics are crucial for ensuring the long-term viability and effectiveness of battery-powered devices and systems.
Capacity Retention
Capacity retention quantifies the battery’s ability to hold its initial charge over time. It is a vital indicator of a battery’s long-term health. Capacity retention is usually expressed as a percentage of the initial capacity. For example, a battery with 80% capacity retention after 1000 cycles indicates that it can still hold 80% of its initial charge after a significant number of charge-discharge cycles.
A lower capacity retention percentage signifies a decrease in the battery’s ability to store energy, leading to shorter operational durations.
Cycle Life
Cycle life refers to the number of complete charge-discharge cycles a battery can endure before its performance degrades below an acceptable threshold. It’s a direct measure of the battery’s durability under repeated use. The testing procedure often involves subjecting the battery to a specific charge-discharge profile for a set number of cycles. Manufacturers commonly specify the number of cycles under standard conditions, such as a constant discharge rate and temperature.
For instance, a battery with a cycle life of 500 cycles indicates its ability to undergo 500 full charge-discharge cycles before its capacity noticeably decreases.
Discharge Rate
Discharge rate evaluates how quickly a battery can deliver its stored energy. A high discharge rate is beneficial for applications requiring rapid energy delivery. The rate is typically expressed in C-rates, where 1C signifies the battery’s discharge capacity in one hour. A 2C discharge rate means the battery can deliver its full capacity in half an hour. Higher discharge rates often correlate with faster performance but can also lead to a faster decline in capacity retention and cycle life.
Testing involves discharging the battery at various C-rates and measuring the corresponding voltage and capacity.
Testing Procedures
Different testing procedures are employed to evaluate battery durability depending on the specific battery type and application.
Battery Type | Testing Procedure |
---|---|
Lithium-ion | Typically involves cycling the battery at various discharge rates and temperatures. Specific testing protocols often involve accelerated aging procedures to shorten the time required for evaluation. For example, a battery might be tested at high temperatures to accelerate degradation. |
Lead-acid | Commonly involves cyclic discharge and charge tests at varying depths of discharge. These tests aim to determine the battery’s ability to maintain its performance during repeated charge-discharge cycles. For example, a battery might be cycled at different discharge rates, and its voltage and capacity would be recorded over time. |
Nickel-metal hydride | Similar to lithium-ion, testing usually involves cycling the battery at different discharge rates and temperatures. Specific protocols may include accelerated aging procedures to predict the battery’s behavior under long-term use. |
Implications on Real-World Applications
The performance metrics directly influence the suitability of batteries for various applications. For example, a battery with high capacity retention and a long cycle life is ideal for portable electronics, while a battery with a high discharge rate is crucial for electric vehicles needing quick acceleration. Understanding these metrics allows engineers to select the most appropriate battery type for a given application, optimizing performance and lifespan.
Materials and Construction
The construction of a durable battery hinges on the careful selection and arrangement of materials. Choosing the right materials directly impacts the battery’s lifespan, performance characteristics, and overall safety. Different materials exhibit varying degrees of resistance to degradation, stress, and chemical reactions, which directly influence the battery’s operational life.A critical aspect of durable battery design is understanding how different materials interact within the battery’s structure.
Material properties, such as thermal conductivity, chemical stability, and mechanical strength, are carefully balanced to optimize the battery’s performance and lifespan. This balance is crucial for achieving high energy density, rapid charge/discharge rates, and extended cycle life.
Material Selection in Different Battery Chemistries
Various battery chemistries employ different materials, each with its own advantages and disadvantages concerning durability. The selection of these materials directly affects the battery’s resistance to degradation.
Durable batteries are crucial for extended use, especially in the latest VR headset market. The latest VR headset models demand longer playtime, which translates to a higher demand for battery tech. Ultimately, the demand for longer battery life in VR headsets will drive innovation in durable battery technology.
- Lithium-ion batteries, a prevalent choice for portable electronics and electric vehicles, commonly use lithium metal or lithium compounds, carbon-based materials (graphite or silicon), and metal oxides (such as cobalt oxide or manganese oxide) in the electrodes. The selection of these materials significantly impacts the battery’s capacity, rate capability, and cycle life. For example, using silicon-based anode materials can improve the energy density of lithium-ion batteries, but it also presents challenges related to volume expansion during charging and discharging cycles.
These challenges need to be addressed through material engineering and advanced manufacturing processes.
- Sodium-ion batteries are emerging as an alternative to lithium-ion batteries due to the abundance and low cost of sodium. Sodium-ion batteries typically utilize sodium metal or sodium compounds in the electrodes. The use of sodium-ion batteries potentially addresses concerns about lithium availability. However, the lower theoretical energy density of sodium compared to lithium necessitates further research into materials and manufacturing processes to improve their performance and durability.
- Solid-state batteries, which are in the developmental stage, utilize solid electrolytes to separate the anode and cathode. This design eliminates the risk of short circuits and enables higher energy densities, but the development of suitable solid electrolytes is a major challenge, directly affecting the battery’s safety and durability. Researchers are working on developing solid electrolytes with high ionic conductivity and mechanical stability to enhance the durability of these batteries.
Advanced Materials and Manufacturing Processes
The durability of batteries can be significantly enhanced through the development and application of advanced materials and manufacturing processes.
- Nanomaterials, such as carbon nanotubes and graphene, offer improved conductivity, mechanical strength, and enhanced surface area, leading to better performance and durability. For example, incorporating graphene into electrode materials can increase the electron transfer rate and improve the battery’s cycle life.
- Advanced coatings and surface treatments can protect electrode materials from corrosion and degradation, extending the battery’s lifespan. Coatings can improve the material’s resistance to mechanical stress and chemical reactions, thereby improving the overall battery performance and longevity.
- Additive manufacturing (3D printing) offers a unique approach to battery manufacturing, allowing for customized battery designs and the incorporation of complex geometries, leading to improved energy density and safety features. 3D printing enables the production of complex electrode structures and battery designs that are difficult or impossible to achieve with traditional methods, which may lead to enhanced durability.
Trade-offs in Material Selection
The selection of materials for durable batteries often involves trade-offs between various characteristics.
- Cost: High-performance materials can be expensive, potentially increasing the overall cost of the battery. Balancing the cost with performance and durability is crucial.
- Availability: The availability of certain materials can influence the scalability of battery production. This is a crucial factor in mass production.
- Environmental Impact: The environmental impact of material extraction and processing must be considered when selecting materials for durable batteries.
Material Composition and Battery Durability
Material Composition | Potential Impact on Durability |
---|---|
High-purity active materials | Improved electrochemical performance, extended cycle life |
Stable electrolyte materials | Enhanced safety, extended cycle life, reduced degradation |
Strong and flexible current collectors | Improved mechanical stability, resistance to mechanical stress, and higher current density |
Advanced coatings | Improved corrosion resistance, extended cycle life |
Environmental Factors
Environmental factors significantly impact the lifespan and performance of batteries. Understanding these factors is crucial for designing durable batteries capable of withstanding various operating conditions. Proper consideration of temperature, humidity, vibration, and storage conditions is essential to maximize battery longevity and reliability.
Temperature Effects
Temperature fluctuations are a primary concern for battery durability. Extreme temperatures can lead to accelerated degradation of the battery’s components. High temperatures can cause electrolyte decomposition and reduce the capacity of the battery, while low temperatures can hinder ion mobility and reduce the discharge rate. This is often seen in lithium-ion batteries where optimal operating temperatures are crucial for peak performance.
For example, prolonged exposure to temperatures above 40°C can drastically shorten the battery’s cycle life in many battery types. Conversely, extremely cold temperatures can impede ion transport, reducing the battery’s ability to deliver power.
Humidity Effects
Humidity levels also play a role in battery performance. High humidity can lead to corrosion of battery components, particularly the metallic components. This corrosion can compromise the integrity of the battery and lead to premature failure. The presence of moisture can also affect the electrical conductivity of the electrolyte, further impacting battery performance.
Vibration Effects
Vibration can cause mechanical stress on the battery’s components, potentially leading to cracks or structural damage, particularly in batteries with delicate internal components. Repeated or high-amplitude vibrations can loosen internal connections, leading to performance degradation and potentially catastrophic failure. This is a critical consideration for batteries used in mobile devices or vehicles.
Storage and Handling
Proper storage and handling procedures are essential to maintaining battery durability. Batteries should be stored in a cool, dry place away from direct sunlight and extreme temperatures. Proper packaging and handling techniques during transportation are also crucial to prevent physical damage. Incorrect storage can lead to accelerated aging and reduced lifespan.
Durable batteries are crucial for today’s tech, especially when considering portability. Modern devices rely heavily on seamless charging, and portable wireless charging solutions like portable wireless charging are becoming increasingly popular. Ultimately, a long-lasting battery is still the best way to ensure consistent device performance, no matter how convenient the charging method.
Designing for Extreme Environments
Battery designs must incorporate strategies to mitigate the impact of extreme environmental factors. This involves using robust materials, employing effective sealing mechanisms, and implementing thermal management systems to control temperature. Advanced materials with improved chemical stability and resistance to corrosion are critical for applications in harsh environments. For example, batteries designed for use in extreme cold climates might incorporate special electrolyte formulations or protective coatings.
Impact of Environmental Factors on Battery Durability
Environmental Factor | Impact on Battery Durability |
---|---|
High Temperature | Accelerated degradation, reduced capacity, shortened cycle life |
Low Temperature | Reduced discharge rate, hindered ion mobility |
High Humidity | Corrosion of components, reduced electrical conductivity |
Vibration | Mechanical stress, potential cracks, performance degradation, internal connection issues |
Improper Storage | Accelerated aging, reduced lifespan |
Applications and Uses
Durable batteries are crucial in a multitude of applications demanding consistent performance and extended lifespan. Their ability to withstand harsh conditions and repeated cycles differentiates them from conventional batteries, making them ideal for specific tasks and environments. This section explores diverse applications, highlighting the suitability of different battery types and the design considerations for ensuring longevity.
Examples of Applications Requiring Durable Batteries
Durable batteries are essential in various applications where reliability and extended lifespan are paramount. These applications range from demanding industrial environments to critical consumer electronics.
- Uninterruptible Power Supplies (UPS): UPS systems require batteries capable of consistently providing power during grid failures. Their durability is critical to ensure uninterrupted operation during outages, protecting sensitive equipment and data. The need for continuous operation and frequent deep discharges necessitates robust battery chemistries.
- Electric Vehicles (EVs): EV batteries must endure numerous charge-discharge cycles, extreme temperatures, and high current demands. Durability is crucial for ensuring long-term performance, safety, and range. Advanced battery designs, including advanced thermal management systems, are crucial for maintaining consistent performance.
- Renewable Energy Storage: Energy storage systems for solar and wind power require batteries that can withstand the variable and intermittent nature of renewable energy sources. These batteries need to endure extended periods of deep discharge and charge, and they require high-cycle life and temperature tolerance. Design considerations often include modularity and scalability.
- Industrial Equipment: Forklifts, mining equipment, and other industrial machinery often operate in harsh environments with frequent starts and stops. Durable batteries are needed for reliable performance, especially in extreme temperatures and high-vibration conditions. These batteries require robust mechanical designs to withstand these demanding conditions.
Battery Type Suitability Based on Durability Needs
The choice of battery type significantly impacts durability. Different chemistries offer varying strengths and weaknesses in terms of cycle life, temperature tolerance, and self-discharge rates.
- Lithium-ion batteries are a prevalent choice due to their high energy density and relatively long cycle life. However, their performance can degrade under extreme temperatures or excessive discharge rates. Specific designs with enhanced thermal management are required for applications with high-temperature fluctuations.
- Lead-acid batteries, despite their lower energy density, are renowned for their robust construction and ability to withstand harsh conditions. Their lower cost and simple design are attractive in some applications. However, their relatively shorter cycle life limits their use in applications demanding high-frequency charging.
- Nickel-metal hydride (NiMH) batteries, while offering good cycle life, have a lower energy density compared to lithium-ion. Their robustness makes them suitable for applications where temperature tolerance is critical and safety is paramount.
Design Considerations for Durable Batteries in Different Applications
Design considerations for durable batteries are application-specific. Key factors include material selection, thermal management, and mechanical robustness.
- Thermal Management Systems: Effective thermal management is critical to prevent overheating and degradation, especially in high-power applications like EVs. Advanced cooling systems and heat dissipation strategies are incorporated to maintain optimal operating temperatures. Proper thermal modeling is essential to predict battery performance in different environmental conditions.
- Robust Mechanical Design: The battery enclosure and internal components must be designed to withstand vibration, shock, and physical stress in applications like industrial equipment. Careful consideration of stress points and material selection is crucial for minimizing failures.
- Material Selection: Choosing appropriate electrode materials, electrolytes, and separators is critical to achieving high-cycle life, good safety, and reliable performance. Materials need to resist corrosion, chemical degradation, and other environmental factors.
Factors Influencing Battery Selection
Several factors influence the selection of batteries for specific tasks and environments. These include the required energy density, power output, cycle life, cost, and environmental impact.
Application | Durability Needs | Suitable Battery Type |
---|---|---|
Electric Vehicles | High cycle life, high energy density, temperature tolerance | Lithium-ion |
Industrial Equipment | High vibration tolerance, robust construction, temperature tolerance | Lead-acid, NiMH |
Renewable Energy Storage | High cycle life, deep discharge capability | Lithium-ion, flow batteries |
UPS | High cycle life, continuous operation | Lithium-ion, Lead-acid |
Testing and Evaluation
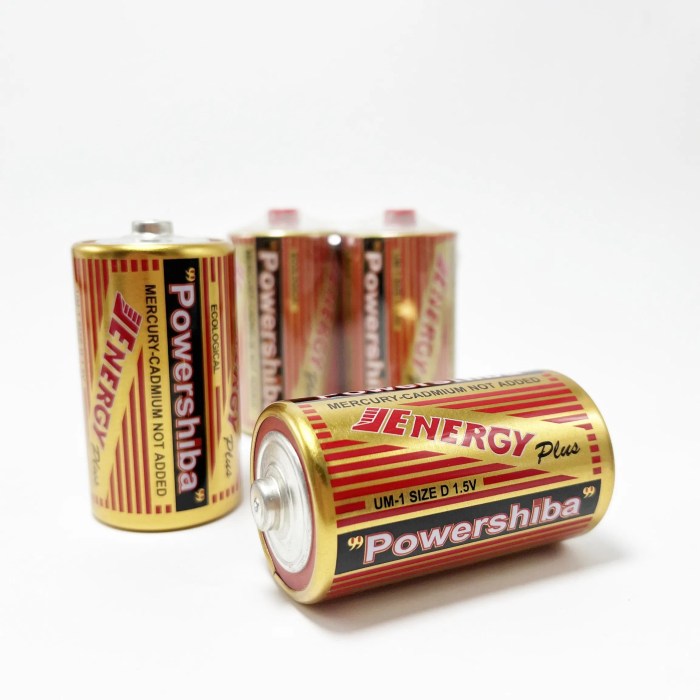
Assessing battery durability is crucial for ensuring reliable performance and longevity. Thorough testing methodologies and adherence to established standards are paramount in evaluating the suitability of battery designs for various applications. This process involves a range of techniques, from accelerated aging simulations to rigorous cycling tests, all designed to uncover potential weaknesses and predict long-term performance.Evaluating battery durability is not just about meeting minimum standards; it’s about identifying the optimal balance between performance and lifespan.
This involves not only assessing the battery’s ability to withstand stress but also its capacity to maintain performance under different conditions. This detailed evaluation is essential for informing design decisions and ultimately, ensuring customer satisfaction.
Various Methods for Testing Battery Durability
A variety of methods are employed to assess battery durability. These methods range from basic discharge/charge cycles to more complex accelerated aging tests, each targeting different aspects of battery performance. Comprehensive testing strategies encompass both laboratory simulations and real-world operational conditions, offering a holistic view of battery resilience.
- Cyclic Testing: This involves repeatedly discharging and charging the battery under controlled conditions. The number of cycles, discharge/charge rates, and depth of discharge are meticulously controlled. This method identifies potential degradation patterns and capacity fading over time.
- Temperature Cycling: Batteries are subjected to varying temperatures to evaluate their performance under extreme conditions. This mimics real-world scenarios where batteries may experience fluctuating temperatures, like those encountered in vehicles or portable electronics. This method helps understand how temperature affects battery life and performance characteristics.
- Accelerated Aging Tests: These tests accelerate the degradation processes to shorten the time required to evaluate the battery’s long-term performance. Factors like elevated temperatures, high discharge/charge rates, or increased cycle counts are employed to simulate the effects of extended use and predict the battery’s lifespan under normal operating conditions.
- Physical Stress Testing: This includes tests like vibration and shock testing, simulating the potential impacts a battery might experience during transportation or use. This ensures the battery can withstand physical stresses and maintain structural integrity.
Standards and Protocols for Evaluating Battery Durability
Standardized protocols and testing standards are crucial for ensuring consistent and reliable evaluations. These standards ensure comparable results across different laboratories and manufacturers, enabling a consistent evaluation process. Examples include industry-recognized standards from organizations like IEC (International Electrotechnical Commission).
- IEC 61960: This standard defines requirements for the testing of rechargeable batteries, covering various aspects, including performance, safety, and environmental considerations. It Artikels specific testing procedures and requirements for reporting results.
- ASTM International Standards: These standards provide guidelines for testing various battery properties, including capacity, rate capability, and cycle life. These tests are widely adopted for battery evaluation and ensure compatibility across different products.
Examples of Standardized Tests and Their Significance
Specific standardized tests provide valuable insights into battery durability. Their significance lies in the ability to quantify performance degradation under controlled conditions, enabling predictions of long-term performance.
Test Name | Significance |
---|---|
Capacity Retention Test: | Measures the battery’s ability to retain its initial capacity over a specified number of cycles. This test is crucial for understanding the rate at which the battery’s capacity degrades. |
Cycle Life Test: | Evaluates the battery’s ability to withstand repeated charge-discharge cycles. This test is critical in determining the battery’s lifespan under normal operating conditions. |
Temperature Cycling Test: | Assesses the battery’s performance at different temperature ranges, identifying how the battery reacts to thermal stresses. This is essential for applications in various climates. |
Role of Quality Control in Ensuring Battery Durability
Quality control plays a vital role in maintaining and improving battery durability. Implementing stringent quality control measures during manufacturing ensures consistency in materials, manufacturing processes, and battery performance. This proactive approach helps minimize variability and maximizes the overall durability of the battery.
Use of Test Results in Making Design Decisions
Test results provide valuable insights for making informed design decisions. By analyzing the data from various tests, engineers can identify areas for improvement in the battery design, materials, and manufacturing processes. This data-driven approach allows for optimization, leading to increased durability and improved performance. For instance, if a specific test reveals that a certain material is prone to degradation, engineers can explore alternative materials or adjust the manufacturing process to mitigate the issue.
Manufacturing Processes
Manufacturing processes play a critical role in determining the durability and performance of batteries. Careful consideration of these processes, from material selection to quality control, significantly impacts the lifespan and reliability of the final product. Optimizing these techniques allows for improved energy density, longer cycle life, and enhanced safety characteristics.
Impact of Manufacturing Techniques on Battery Performance
Different manufacturing techniques exert varying degrees of influence on battery performance and lifespan. Factors like the precision of electrode deposition, the uniformity of electrolyte distribution, and the sealing methods all contribute to the overall durability of the battery. The quality of the materials used and the precision of the manufacturing processes are critical for achieving the desired performance characteristics.
Innovative Manufacturing Techniques for Enhancing Durability
Several innovative manufacturing techniques are emerging to improve battery durability. Nanotechnology plays a crucial role in creating high-surface-area electrodes, leading to enhanced electrochemical reactions and increased energy storage capacity. Advanced coating techniques and optimized electrolyte formulations contribute to improved safety and reduced degradation rates. For example, employing additive manufacturing (3D printing) for electrode fabrication can allow for intricate designs, tailoring electrode properties for specific applications.
Quality Control in Battery Manufacturing, Durable battery
Robust quality control measures are essential to ensure battery durability throughout the manufacturing process. Strict adherence to specifications during material selection, electrode preparation, cell assembly, and sealing is crucial. Regular testing at various stages, including performance, safety, and environmental stress tests, is vital to identify and correct potential issues. Automated testing systems can significantly increase efficiency and consistency in quality control.
Summary of Manufacturing Techniques and their Impact
Manufacturing Technique | Impact on Battery Durability |
---|---|
Nanomaterial incorporation | Enhanced electrode surface area, improved electrochemical performance, increased energy density. |
Advanced coating techniques | Improved electrolyte stability, reduced corrosion, extended cycle life. |
Optimized electrolyte formulations | Enhanced ionic conductivity, improved safety characteristics, reduced degradation. |
Additive Manufacturing (3D Printing) | Precise electrode design, customized electrode properties, potentially reduced manufacturing cost. |
Automated testing systems | Increased testing efficiency, improved consistency in quality control, early detection of defects. |
Future Trends
The future of durable battery technology hinges on innovative approaches to materials, manufacturing, and testing. Ongoing research and development are actively pursuing solutions to address the limitations of current designs, aiming for enhanced performance, safety, and cost-effectiveness. This exploration promises a significant impact on various sectors, including electric vehicles, portable electronics, and grid-scale energy storage.
Material Advancements
Materials science plays a crucial role in improving battery durability. Researchers are exploring a wide range of novel materials to replace or augment existing components, enhancing their performance and longevity. This involves investigating new electrode materials, electrolytes, and separators. For instance, transition metal oxides and sulfides are being studied for their potential to increase energy density and improve cycle life.
Solid-state electrolytes, which promise higher safety and energy density, are also a key area of focus.
Manufacturing Process Innovations
Optimizing manufacturing processes is essential for scaling up production and reducing costs while maintaining quality. Advanced techniques, such as 3D printing and nanotechnology, are being integrated into battery production. 3D printing allows for customized battery designs and potentially improved material utilization, reducing waste. Nanotechnology offers the possibility of creating highly efficient and durable battery components. This could lead to lighter, more compact batteries, reducing overall weight and increasing energy density in portable applications.
Testing and Evaluation Methodologies
Current testing methodologies for battery durability are often insufficient to fully capture the complexities of real-world use. Researchers are working on developing more sophisticated and accelerated testing protocols. This involves employing advanced characterization techniques, such as electrochemical impedance spectroscopy, to monitor battery degradation mechanisms. Simulation models are also being employed to predict long-term performance and durability, allowing for more effective optimization and development.
Emerging Trends and Technologies
Several emerging trends hold the potential to revolutionize battery durability. One such trend is the development of adaptive battery management systems. These systems monitor the battery’s state in real-time and adjust charging and discharging parameters dynamically, optimizing performance and extending lifespan. Furthermore, the incorporation of artificial intelligence (AI) in battery design and manufacturing is anticipated to accelerate the discovery of novel materials and processes, improving efficiency and quality.
Future Prospects and Applications
These advancements in materials, manufacturing, and testing are expected to lead to batteries with significantly improved durability and performance. Applications include electric vehicles with extended range and fast charging capabilities, portable electronics with longer battery life, and grid-scale energy storage systems with enhanced reliability and lifespan. Ultimately, this will contribute to a more sustainable and efficient energy landscape, with applications spanning transportation, consumer electronics, and energy infrastructure.
Durability vs. Cost: Durable Battery
Balancing durability and cost is a critical aspect of battery technology. Optimizing battery performance while keeping the price competitive is a constant challenge. The trade-offs involved in these decisions often dictate the viability and widespread adoption of new battery technologies.Different approaches to battery design and materials will impact both durability and cost. Exploring cost-effective strategies to enhance durability without compromising performance is essential for wider market penetration and broader accessibility.
Cost Implications of Durable Battery Solutions
Various durable battery solutions exhibit varying price points. Lithium-ion batteries, a prevalent choice, offer good energy density but their production costs can fluctuate based on material availability and manufacturing processes. Advanced battery chemistries, while potentially enhancing durability, may involve specialized materials and complex manufacturing techniques, increasing the overall cost. Furthermore, the use of high-strength, corrosion-resistant materials in the battery casing can contribute to increased costs.
Cost-Effective Strategies for Improving Battery Durability
Several strategies can enhance battery durability without significant cost increases. Optimizing the battery’s internal structure through improved electrode designs and electrolyte formulations can improve cycle life without necessarily adding expensive materials. Implementing robust quality control measures during manufacturing and utilizing existing, proven materials in new configurations can also reduce the cost of achieving high durability. Furthermore, the use of more efficient and less expensive manufacturing processes can also contribute to lowering the cost of a durable battery.
Trade-offs Between Durability and Cost
A crucial trade-off exists between durability and cost. Higher durability often necessitates more robust materials or complex designs, leading to increased costs. Conversely, cost-conscious designs may compromise durability, reducing the battery’s lifespan and overall performance. The optimal balance between these two factors depends on the specific application and the user’s priorities.
Relationship Between Material Cost and Battery Durability
The cost of battery materials plays a significant role in determining the overall battery durability. Using less expensive materials may result in reduced durability, while incorporating high-cost, high-performance materials can increase durability but also increase the battery’s price. The relationship is not linear; it often depends on the specific application, the desired level of durability, and the interplay between different material properties.
Correlation Between Durability and Cost
Durability Level | Estimated Cost | Material Considerations |
---|---|---|
Low | Low | Common, readily available materials |
Medium | Medium | Improved material configurations, slightly more complex processes |
High | High | Advanced materials, specialized manufacturing processes, robust designs |
This table provides a general overview. Specific cost-durability relationships vary significantly depending on the specific battery chemistry, application requirements, and manufacturing processes.
Safety Considerations
Durable batteries, while offering significant advantages, necessitate careful consideration of potential hazards. Their high energy density and chemical composition introduce safety risks that must be proactively addressed throughout the entire lifecycle, from manufacturing to end-of-life disposal. Understanding and mitigating these risks is crucial for both the safety of users and the wider public.
Safety Concerns Associated with Durable Batteries
Durable batteries, with their higher energy density, pose specific safety risks compared to conventional batteries. These risks include thermal runaway, short circuits, and the potential for hazardous material release. Improper handling or manufacturing processes can lead to these issues, posing serious threats to personnel and the surrounding environment. The potential for fire or explosion underscores the critical need for robust safety protocols.
Safety Measures During Manufacturing
Implementing rigorous safety measures during the manufacturing process is paramount. This involves using appropriate personal protective equipment (PPE), adhering to strict handling procedures for hazardous materials, and utilizing advanced safety equipment like explosion-proof enclosures and fire suppression systems. Furthermore, regular safety training for all personnel involved in the manufacturing process is essential to prevent accidents and ensure compliance with safety regulations.
Safety Measures During Use
Appropriate safety measures during the use phase are equally critical. Users must be informed about potential hazards, such as the risk of overheating or leakage. Clear instructions on proper charging, storage, and handling procedures should be provided. Strict adherence to these guidelines can prevent accidents and injuries. Monitoring battery performance and implementing safety mechanisms, like thermal management systems, is also crucial.
Safety Measures During Disposal
Proper disposal procedures are vital to prevent environmental contamination and ensure public safety. Recycling and proper handling of spent batteries are critical. The presence of hazardous materials necessitates careful handling to prevent environmental contamination. Batteries must be disposed of in accordance with local regulations and guidelines, ensuring the safe and responsible management of potentially harmful substances.
Safety Regulations and Standards
Several international and national safety regulations and standards govern the design, manufacture, and use of durable batteries. These standards Artikel specific requirements for safety testing, labeling, and documentation. Compliance with these standards is essential to ensure public safety and protect the environment. Examples include UL (Underwriters Laboratories) standards and relevant IEC (International Electrotechnical Commission) standards.
Importance of Safety in Development and Deployment
Prioritizing safety in the development and deployment of durable battery solutions is not just a matter of compliance but a critical aspect of responsible innovation. Safety considerations must be integrated into every stage of the design process, from initial material selection to final product testing. This proactive approach ensures the safe operation and longevity of the battery solution.
Table Summarizing Safety Considerations for Different Battery Types
Battery Type | Thermal Runaway Risk | Short Circuit Risk | Hazardous Material Release | Disposal Considerations |
---|---|---|---|---|
Lithium-ion | High | Medium | Moderate (depending on specific chemistry) | Strict recycling/disposal protocols required |
Sodium-ion | Lower than Li-ion | Medium | Moderate (depending on specific chemistry) | Recycling/disposal protocols similar to Li-ion |
Solid-state | Lower than Li-ion | Low | Low (often inorganic) | Recycling/disposal protocols may be simplified |
Outcome Summary
In conclusion, durable batteries are crucial for a wide range of applications, from portable electronics to electric vehicles. Understanding their diverse characteristics, performance metrics, and environmental considerations is vital for selecting the right battery for a specific need. This guide has provided a thorough overview, offering insights into the future of battery technology and the ongoing quest for even more reliable and efficient power solutions.
Questions Often Asked
What are the key factors that affect a battery’s lifespan?
Several factors influence battery lifespan, including the battery chemistry, environmental conditions (temperature, humidity), manufacturing quality, and usage patterns (number of charge cycles, depth of discharge). Proper storage and handling also play a significant role.
How can I choose the right battery for my specific application?
Selecting the appropriate battery depends on the application’s specific requirements. Factors to consider include the desired capacity, discharge rate, cycle life, environmental conditions, and safety standards. A thorough understanding of the performance metrics of different battery types is crucial.
What are some emerging trends in durable battery technology?
Emerging trends include advancements in battery materials, manufacturing processes, and testing methodologies. Research focuses on improving energy density, cycle life, and safety features. Solid-state batteries and other novel chemistries are gaining traction.
What are the safety precautions for handling and using durable batteries?
Safety is paramount. Proper handling, storage, and disposal procedures should be followed to mitigate risks. Manufacturers and users should adhere to safety regulations and standards to prevent accidents and ensure the safe operation of durable battery systems.