High-end water resistant defines the cutting edge of waterproof technology, exploring how extreme conditions are met with sophisticated engineering. From rugged watches to high-tech phone cases, this deep dive reveals the intricacies of design, materials, and manufacturing processes that guarantee lasting protection.
This exploration examines the different standards and certifications, highlighting the technological advancements that drive high-end water resistance. We’ll look at the materials used, comparing different approaches to sealing and protection, from gaskets to advanced coatings. The discussion further delves into design considerations, testing methods, and the cost-benefit analysis of achieving this level of water resistance.
Defining High-End Water Resistance
High-end water resistance transcends basic protection from splashes. It signifies a robust design capable of withstanding significant water exposure in diverse scenarios, from deep dives to heavy downpours. This level of protection requires meticulous engineering and the application of advanced materials and technologies. The criteria for “high-end” vary across different product categories, demanding specific standards to ensure user confidence and safety.High-end water resistance is characterized by its ability to withstand prolonged exposure to water, exceeding the capabilities of standard or lower-tiered water resistance.
This superior performance is achieved through advanced engineering principles and rigorous testing, ensuring the protection of sensitive internal components or the user from water damage in demanding situations.
Water Resistance Standards and Certifications
Understanding the different standards and certifications is crucial for evaluating the true water resistance capabilities of a product. These standards provide a consistent framework for assessing and comparing products, ensuring a reliable level of protection. Various organizations, such as the International Electrotechnical Commission (IEC), develop and maintain these standards. A common example is the IPX rating system, which categorizes the degree of water protection based on different conditions.
- IPX Ratings: The IPX rating system provides a standardized method for classifying the water resistance of electronic devices and other products. The first digit indicates protection from solid objects (dust, debris) and the second digit indicates protection from water ingress. Higher numbers signify a greater level of protection. For instance, an IPX8 rating indicates protection against submersion in water, a critical factor for devices like smartwatches and diving watches.
- Specific Certifications: Beyond general IPX ratings, specific certifications, such as those issued by the Swiss watchmaking industry for high-end watches, often include more detailed and rigorous testing procedures. These certifications validate the watch’s ability to withstand extreme water pressure, ensuring its reliability and performance under demanding conditions.
Technological Advancements in Water Resistance
Technological advancements in materials and sealing techniques have significantly improved the water resistance of various products. Innovative designs and manufacturing processes are constantly pushing the boundaries of what’s possible, ensuring superior protection in increasingly challenging environments.
- Advanced Sealing Technologies: Sophisticated sealing technologies play a pivotal role in achieving high-end water resistance. These techniques involve the use of specialized gaskets, polymers, and other materials that create an airtight barrier to prevent water penetration. For example, advanced ceramic coatings or specialized polymers are used in high-end watch cases to create a nearly impenetrable seal against water.
- Material Innovations: The development of new and improved materials has also contributed to the enhancement of water resistance. High-end watch manufacturers often use materials like titanium, sapphire crystal, and specialized alloys that offer exceptional durability and resistance to water damage. Phone cases, for example, use reinforced polymers with a higher level of water resistance to safeguard internal components.
Materials Used for High-End Water Resistance
Different materials are used to achieve high-end water resistance, each with unique properties that contribute to the overall protection of the product. The choice of material often depends on the specific application and the desired level of protection.
- Metals: Metals like titanium and stainless steel, renowned for their durability and corrosion resistance, are frequently used in high-end watches and other water-resistant devices. Their strength and density help maintain a watertight seal.
- Polymers: Advanced polymers, including reinforced polymers and specialized resins, are commonly used in phone cases and other water-resistant products. These materials are often designed to be lightweight and offer exceptional protection from water damage. Specific polymers can be used in the production of water-resistant garments, providing a reliable barrier against water penetration.
Comparing High-End Water Resistance Technologies
High-end water resistance in products like watches and smartphones relies on sophisticated techniques that go beyond simple waterproofing. These methods ensure prolonged functionality and user experience even in demanding conditions. Understanding these technologies is crucial for discerning quality and reliability.Various approaches contribute to high-end water resistance. These include meticulous sealing, strategically placed gaskets, and specialized coatings. Each method has its own set of advantages and limitations, impacting the overall performance and durability of the final product.
Sealing Techniques
Sealing techniques are fundamental to high-end water resistance. They involve creating an airtight barrier around critical components, preventing water intrusion. Precisely engineered seals, often using specialized polymers or ceramics, are crucial for a robust barrier against water. Careful consideration of the materials and their interaction with the environment are key. For instance, materials resistant to corrosion and degradation in high-humidity conditions are preferred.
Gasket Applications
Gaskets are crucial components in high-end water-resistant designs. Strategically placed gaskets create a watertight seal around joints and openings. The material selection for gaskets is critical; flexible, resilient materials are preferred for their ability to adapt to different shapes and sizes. The precision in their placement and the quality of the material used directly affect the device’s overall water resistance rating.
For example, O-rings, a common type of gasket, are widely used for their reliability and ability to maintain a consistent seal.
Special Coatings
Specialized coatings provide an additional layer of protection against water intrusion. These coatings are often applied to exterior surfaces, creating a hydrophobic barrier. The effectiveness of these coatings depends on their chemical composition and application method. Coatings that resist abrasion and weathering are preferred. Furthermore, coatings that self-repair minor surface damage are advantageous in long-term use.
For instance, some coatings utilize nano-scale structures to repel water effectively.
Durability Comparison Table
Material | Advantages | Disadvantages | Durability (Estimated) |
---|---|---|---|
Silicone Rubber | Excellent flexibility, good chemical resistance, relatively inexpensive | Can degrade over time in extreme temperatures, not as strong as some other materials | Good, suitable for mid-range to high-end applications |
Elastomeric Polymers | High tensile strength, good flexibility, good temperature resistance | Can be more expensive than silicone rubber, may require more precise manufacturing | Excellent, suitable for high-end applications requiring maximum durability |
Ceramic | Exceptional hardness, high temperature resistance, very durable | Can be brittle, potentially more expensive than other materials | Excellent, suitable for high-end applications requiring extreme durability and resistance to wear and tear |
Note: Durability ratings are estimations based on typical applications and performance characteristics. Actual durability may vary depending on specific product design and environmental conditions.
Design Considerations for High-End Water Resistance
High-end water resistance isn’t simply about adding a few seals; it’s a meticulous design process that considers numerous factors from material selection to manufacturing precision. Achieving exceptional water resistance requires a holistic approach, integrating various elements to ensure durability and performance in challenging environments. This section delves into the crucial design aspects that underpin the superior water resistance found in premium products.
Testing the Effectiveness of Water-Resistant Materials
Rigorous testing is paramount to validating the water resistance of materials. A comprehensive testing method involves subjecting samples of various materials to controlled, extreme conditions. This includes simulating pressures exceeding those encountered in typical use cases. For instance, submerging samples in pressurized water tanks at varying depths and temperatures allows engineers to observe material performance under duress.
Data collected during these tests aids in selecting the most suitable materials and identifying potential weaknesses.
Impact of Product Design on Water Pressure Resistance
The design of a product directly influences its ability to withstand water pressure. Strategic placement of seals and gaskets, the shape of housings, and the material’s inherent properties are crucial design considerations. Consider a dive watch case; its rounded, streamlined shape minimizes the surface area exposed to water pressure, while specialized gaskets effectively seal critical components, preventing water ingress.
Properly designed enclosures minimize stress points and concentrate pressure on reinforced areas.
Precision Tolerances and Manufacturing Processes
Precise tolerances and stringent manufacturing processes are critical for achieving high-end water resistance. Tiny gaps or imperfections can compromise a product’s water resistance, allowing water to seep in. Manufacturers employ advanced quality control measures, such as laser-guided machining and precision assembly, to maintain tight tolerances. This ensures the consistent effectiveness of seals and gaskets, preventing leaks and maintaining the intended water resistance rating.
Influence of Design Elements on Water Resistance
The following table highlights the various design elements that directly influence a product’s water resistance:
Design Element | Description | Impact on Water Resistance |
---|---|---|
Material Selection | Choosing materials with high water-resistance properties | Determines the material’s ability to resist penetration |
Seal Design | Strategic placement and construction of seals and gaskets | Creates a barrier against water intrusion |
Enclosure Shape | Optimized shape of the product’s housing | Reduces pressure points and minimizes surface area exposed to water |
Tolerance Management | Ensuring tight tolerances during manufacturing | Prevents leaks and maintains integrity of seals |
Manufacturing Processes | Implementing precision machining and assembly methods | Ensures consistency and accuracy in creating watertight seals |
Applications of High-End Water Resistance
High-end water resistance is no longer a luxury but a crucial feature in a wide range of products. From the depths of the ocean to the rugged outdoors, this technology ensures reliable performance and safety in challenging environments. This section explores the diverse applications of high-end water resistance, highlighting its importance and the unique requirements in each context.High-end water resistance transcends simple waterproofing.
It encompasses sophisticated engineering and material science, resulting in products that can withstand extreme pressure and prolonged immersion. This allows for a wider range of usage and guarantees functionality even under adverse conditions.
Diving Watches
Diving watches are a prime example of the necessity for high-end water resistance. These timepieces need to withstand considerable pressure at significant depths. The specific requirements for high-end water resistance in diving watches include a robust case design, a meticulously sealed crown, and gaskets engineered for reliable sealing against water intrusion. Furthermore, the materials used in the watch’s construction, such as sapphire crystal and corrosion-resistant metals, play a vital role in maintaining the watch’s functionality and appearance even at extreme depths.
The watch’s ability to accurately display time underwater is critical for the diver’s safety. A faulty or inaccurate reading can lead to errors in dive planning and execution, posing a significant risk. Thus, the need for exceptional water resistance in diving watches is paramount for safety and precision.
Waterproof Smartphones
The increasing demand for mobile devices in water-exposed environments has spurred the development of waterproof smartphones. These devices require specialized sealing and protective layers to prevent water damage, ensuring functionality during activities like swimming or near water sources. For high-end waterproof smartphones, the emphasis is on durability and reliability. This often involves utilizing advanced sealing technologies, employing multiple layers of waterproofing, and incorporating robust internal components that can withstand moisture without compromise.
The use of specialized materials in the construction of these devices is critical, with a focus on resistance to corrosion and the protection of electronic components from water damage.
Outdoor Clothing
High-end outdoor clothing, designed for activities like hiking and climbing, necessitates high water resistance. The key to high-end water resistance in outdoor clothing lies in the fabric construction. This includes specialized waterproof and breathable materials that prevent water penetration while allowing moisture vapor to escape. These fabrics are typically treated with durable water repellent (DWR) coatings, which create a barrier against water, preventing it from seeping into the clothing.
The need for breathability in such clothing is critical for maintaining comfort and preventing overheating during physical activity. Thus, the high-end water resistance in outdoor clothing is designed to protect the wearer from the elements while maintaining comfort and performance.
Materials for High-End Water Resistance
High-end water resistance in products necessitates careful selection of materials that can effectively withstand exposure to water and moisture. The performance of these materials plays a critical role in achieving the desired level of protection, and this selection process is paramount to the final product’s success. This section will delve into the essential properties of materials, their importance, and examples of high-end materials used in water-resistant products.
Essential Material Properties, High-end water resistant
The primary properties crucial for high-end water resistance include impermeability, durability, and aesthetic appeal. Impermeability prevents water from penetrating the material, while durability ensures the material retains its protective qualities over time. Aesthetic considerations are equally important, as high-end products often demand sophisticated designs that are compatible with the chosen material’s qualities. The successful integration of these properties is vital for the creation of a truly water-resistant product.
Importance of Material Selection
Material selection significantly impacts the overall water resistance of a product. The correct choice of material ensures that the product can effectively resist water penetration and maintain its integrity under various conditions. Incorrect material selection can lead to leaks, damage, or a reduction in the product’s lifespan, which is unacceptable in high-end applications. Careful material selection directly correlates with the product’s ability to function as intended in wet environments.
Examples of High-End Materials
Various high-end materials exhibit exceptional water resistance. These materials often combine superior impermeability with aesthetic qualities, making them suitable for high-end products. Examples include:
- Titanium alloys: These alloys are exceptionally strong and lightweight, making them ideal for high-end watches and other precision instruments. Their inherent resistance to corrosion is a key advantage in water-resistant applications.
- High-grade ceramics: Known for their exceptional hardness and durability, ceramics are used in high-end watches and jewelry. They provide superior resistance to scratching and water penetration.
- Carbon fiber composites: These materials offer exceptional strength-to-weight ratios, which is critical in designing high-end water-resistant products like sports equipment. Their water resistance can be further enhanced with specialized coatings.
- Advanced polymers: Specific polymers are engineered for superior water resistance and flexibility. They are utilized in waterproof clothing, bags, and other outdoor gear, where resilience and functionality are key factors.
Comparative Analysis of Material Properties
The following table summarizes the water resistance properties of different materials. This comparative analysis highlights the unique characteristics of each material, offering valuable insights for designers seeking to create highly water-resistant products.
Material | Impermeability | Durability | Aesthetic Appeal | Cost |
---|---|---|---|---|
Titanium Alloy | Excellent | High | Sophisticated | High |
High-Grade Ceramics | Excellent | Very High | Elegant | Very High |
Carbon Fiber Composite | Good (with coatings) | High | Modern | Medium-High |
Advanced Polymers | Excellent (depending on type) | Moderate to High | Variable | Medium |
Manufacturing Processes for High-End Water Resistance
High-end water-resistant products demand meticulous manufacturing processes that ensure consistent performance and durability. These processes must incorporate rigorous quality control measures to maintain the product’s integrity and achieve the desired level of protection. The manufacturing techniques must also adapt to the specific material and design choices, ultimately leading to a high-end product.The complexity of creating water-resistant products extends beyond simply applying a coating.
A comprehensive understanding of material science, sealing techniques, and manufacturing precision is paramount. This includes careful consideration of the materials’ properties, the application methods, and the potential for defects. Manufacturing processes are not just about achieving a water-resistant outcome, but also about consistently producing that outcome across a large volume of products.
Quality Control in Manufacturing
Rigorous quality control is essential for maintaining the high-end standards of water resistance. This involves a multi-stage process that includes inspections at various points during the manufacturing process. Testing for water penetration is performed using standardized methods, ensuring that the products meet or exceed the required water resistance levels. This includes testing different parts of the product under different pressure and time conditions to ensure consistent protection.
Challenges in Mass Production
Maintaining consistent high-end water resistance across mass production presents significant challenges. Variations in material properties, inconsistencies in application processes, and the inherent limitations of automated systems can lead to inconsistencies in water resistance. For example, variations in the thickness of a sealing layer, slight imperfections in the manufacturing of the housing, or inconsistent pressure during the sealing process can affect the final outcome.
Innovative Manufacturing Techniques
Innovative manufacturing techniques play a crucial role in achieving high-end water resistance. For example, advanced sealing technologies, such as ultrasonic welding for intricate joints, can create a virtually airtight seal. Nanotechnology-based coatings with enhanced water-repellent properties, and precise robotic application of sealing materials are further examples of innovations.
Specific Manufacturing Procedures
The specific manufacturing procedures for water-resistant products vary depending on the material and design. For instance, creating a water-resistant watch involves multiple layers of gaskets, seals, and coatings, while a water-resistant smartphone necessitates the use of sealant around all openings and components. The process often involves multiple steps, from initial material preparation to final sealing and testing.
- Material Preparation: Careful selection and preparation of materials, such as the use of high-purity metals or specialized polymers, are critical for ensuring consistent water resistance. This might include cleaning, pre-treatments, and precise cutting/shaping.
- Sealing Application: Accurate and consistent application of sealing materials, like adhesives or polymers, is vital for preventing water ingress. Techniques include specialized application equipment and controlled environments to maintain consistent quality.
- Assembly Procedures: Proper assembly of components and precise alignment are crucial to prevent leaks. This may involve robotic assembly lines or manual techniques, with specific quality checks at each step.
- Testing and Validation: Rigorous testing protocols are employed to verify the water resistance levels. This often involves submersion tests in controlled environments and pressure testing to evaluate the performance under different conditions.
Importance of Material Selection
The choice of materials directly impacts the product’s water resistance. High-end water resistance necessitates using materials with excellent water-repellent properties and durability. Materials such as specialized polymers with hydrophobic coatings, or high-grade metals with corrosion resistance, are key.
Testing and Evaluation of High-End Water Resistance
Thorough testing is critical for validating the water resistance claims of high-end products. Rigorous protocols, encompassing various methods and standardized procedures, are essential to ensure the reliability and durability of these items in challenging aquatic environments. The testing process goes beyond simple submersion, delving into the long-term effects of water exposure and pressure variations.Precise and standardized testing methodologies are crucial to ensure consistent and reliable evaluations of water resistance.
Such standards provide a benchmark for manufacturers and consumers alike, promoting transparency and allowing for meaningful comparisons across different products. The use of standardized testing protocols helps in comparing performance characteristics, facilitating informed purchasing decisions.
Methods for Evaluating Water Resistance
Various methods are employed to evaluate water resistance, each targeting specific aspects of the product’s performance. These methods can be broadly categorized as short-term and long-term assessments, each serving distinct purposes. Short-term tests typically involve rapid submersion, pressure, or spray tests, while long-term tests simulate real-world conditions over extended periods.
Standardized Testing Procedures
Standardized testing procedures are paramount in ensuring consistent and reliable results. These procedures define the specific conditions under which tests are conducted, including parameters like water temperature, pressure, duration, and materials used. The adoption of internationally recognized standards like those from the International Organization for Standardization (ISO) or other relevant industry bodies ensures that results are comparable across different manufacturers and testing laboratories.
Examples of Rigorous Testing Protocols
High-end water resistance testing often involves complex protocols, exceeding basic submersion tests. These protocols might include subjecting the product to controlled pressure changes in a pressure chamber to mimic deep-sea conditions. They might also involve cyclic exposure to water, saltwater, or various temperature ranges, mirroring the effects of repeated exposure to different aquatic environments. Another example could be a long-term spray test where the product is exposed to a controlled spray of water for an extended period.
High-end water resistance is crucial for electronic devices, especially when considering the components like circuit boards. A thorough understanding of how these components function, like those reviewed in detail in circuit board review , is vital for achieving the desired level of protection. This ultimately ensures the long-term reliability of the high-end water resistant devices.
This simulates continuous exposure in a variety of environments.
Summary of Testing Methods
Testing Method | Description | Applications |
---|---|---|
Submersion Test | The product is submerged in water under specified pressure and temperature for a set duration. | Assessing general water resistance, depth rating |
Pressure Test | The product is subjected to controlled pressure changes to simulate deep-water environments. | Evaluating performance at various depths, pressure resistance |
Spray Test | The product is exposed to a controlled spray of water, typically for an extended period, to simulate continuous exposure. | Evaluating resistance to prolonged wetness, water penetration |
Saltwater Immersion Test | The product is submerged in saltwater under specific conditions to assess its resistance to corrosion. | Assessing durability in saltwater environments, evaluating corrosion resistance |
Cyclic Testing | The product is subjected to repeated cycles of submersion, drying, and exposure to different conditions. | Assessing long-term durability, performance under fluctuating conditions |
Cost Considerations in High-End Water Resistance
High-end water resistance, while enhancing product value and appeal, introduces complexities in cost management. Factors such as material selection, manufacturing processes, and testing protocols significantly influence the price point. Understanding these cost drivers is crucial for product development and pricing strategies.Achieving superior water resistance often involves a trade-off between performance and cost. Sophisticated materials and meticulous manufacturing techniques may result in higher production costs, but they guarantee a premium level of protection and durability.
Conversely, simpler solutions, while potentially less expensive, might compromise the long-term performance and perceived value of the product.
Material Selection and Cost
Materials play a pivotal role in determining the cost of achieving high-end water resistance. Different materials exhibit varying degrees of water impermeability and resistance to pressure, leading to diverse pricing structures. For example, high-quality, specialized polymers often command a premium price compared to standard materials. Likewise, the use of advanced, corrosion-resistant metals can elevate the overall cost.
- Precious metals like titanium and platinum, often employed in high-end watches and jewelry, offer exceptional corrosion resistance and aesthetic appeal, but their higher cost is a significant consideration.
- Advanced ceramics and composites, while possessing exceptional strength and durability, can be more expensive than traditional materials.
- Specialized sealants and gaskets, meticulously designed for watertightness, can also significantly impact the cost, particularly when multiple layers are required for extreme conditions.
Manufacturing Processes and Cost
The complexity of manufacturing processes directly impacts the cost of high-end water resistance. Techniques like specialized sealing, multiple layers of reinforcement, and precise machining contribute to higher production costs. Labor costs associated with these specialized processes can be substantial, especially for intricate designs.
- Multi-stage sealing procedures, often requiring specialized equipment and highly skilled labor, can drive up production costs.
- Advanced machining techniques, like laser welding or precision molding, are frequently employed to create watertight joints and ensure the integrity of the product, but they often result in higher equipment costs and potential higher labor costs.
- The use of automated systems, while potentially reducing labor costs in certain instances, can still add to the initial investment in specialized machinery.
Water Resistance Technology Comparison
Different water-resistant technologies offer varying levels of protection and cost-effectiveness. The choice of technology is often driven by the specific application and desired level of water resistance. For instance, the technology utilized in high-end dive watches differs considerably from that employed in high-end smartphone designs.
- Multi-layer construction, incorporating various materials with specific properties, can achieve higher levels of water resistance but increases complexity and costs.
- Advanced sealing mechanisms, employing specialized gaskets and seals, often enhance the water resistance performance, but their production and integration costs are elevated.
- Vacuum sealing techniques are often employed for high-end products, which contribute to the premium price tag due to the specialized equipment and process requirements.
Cost-Effectiveness Comparison Table
Technology | Description | Cost Effectiveness |
---|---|---|
Multi-layer construction | Multiple layers of materials for enhanced water resistance | Medium to high |
Advanced sealing mechanisms | Specialized gaskets and seals for tighter integration | High |
Vacuum sealing | Creating a vacuum-sealed environment | Very high |
Surface treatments | Chemical or physical treatments to enhance water resistance | Medium |
Sustainability in High-End Water Resistance: High-end Water Resistant
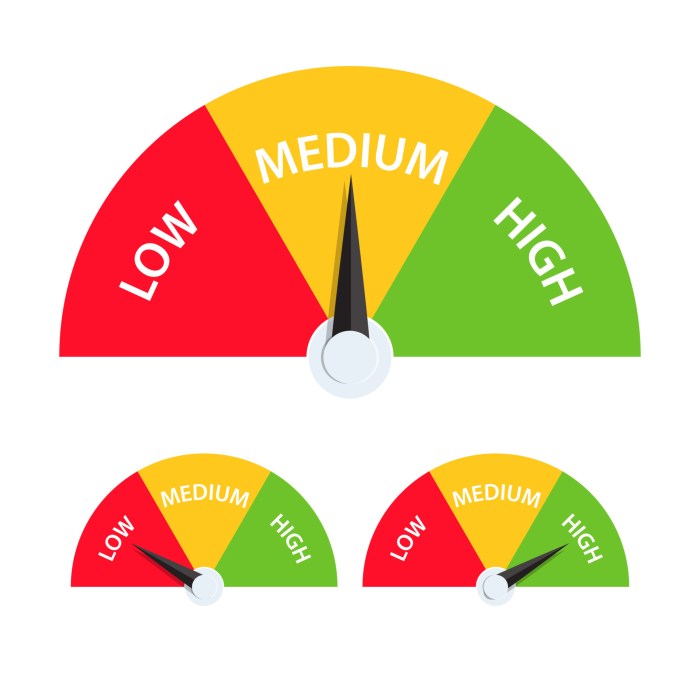
High-end water-resistant products, while often lauded for performance and luxury, frequently face scrutiny regarding their environmental impact. The materials and manufacturing processes employed can have significant effects on the planet. Addressing these concerns is crucial for maintaining the appeal and desirability of these products in a world increasingly focused on sustainable practices.Understanding the environmental footprint of materials and production methods is vital for creating truly sustainable high-end water-resistant products.
This involves a shift from traditional, resource-intensive materials towards more eco-friendly alternatives, coupled with responsible manufacturing practices.
Environmental Impact of Materials
The production and use of conventional materials for high-end water resistance often involve substantial environmental costs. Materials like certain alloys, specific plastics, and rare earth elements may be sourced from environmentally sensitive regions, leading to deforestation, habitat destruction, and pollution. Furthermore, the energy consumption during extraction, processing, and manufacturing can be significant, contributing to greenhouse gas emissions.
Sustainable Material Incorporation
Several sustainable alternatives are available to mitigate the environmental impact. Recycled materials, bio-based polymers, and responsibly sourced metals can be effectively incorporated into the design of high-end water-resistant products. This approach reduces reliance on virgin resources, lessening the strain on ecosystems. Furthermore, advancements in material science allow for the development of high-performance materials with a lower environmental footprint.
Examples of Sustainable Practices
High-end brands are beginning to adopt sustainable practices in water-resistant design. For example, some manufacturers are incorporating recycled plastics into outer shells or using bio-based polymers for gaskets and seals. This minimizes the environmental impact while maintaining the desired level of performance. Another example is the utilization of renewable energy sources during the manufacturing process.
Eco-Friendly Material Comparison
Material | Water Resistance Properties | Sustainability Advantages |
---|---|---|
Recycled Aluminum | Excellent corrosion resistance, high tensile strength, and good water resistance. | Reduces the need for mining virgin aluminum, lowering energy consumption and carbon footprint. |
Bio-based Polyurethane | High elasticity, durability, and excellent water resistance. | Derived from renewable resources, reducing dependence on fossil fuels and promoting carbon sequestration. |
Recycled Carbon Fiber | Exceptional strength-to-weight ratio, and good water resistance. | Reduces the demand for virgin carbon fiber, lessening the need for significant energy consumption and resource depletion. |
Bamboo | Good tensile strength and water resistance properties. | A rapidly renewable resource, requiring less water and pesticides compared to other wood sources. |
Future Trends in High-End Water Resistance
High-end water resistance is constantly evolving, driven by technological advancements and consumer demand for increasingly durable and sophisticated products. This evolution necessitates a keen understanding of emerging technologies, material innovations, and manufacturing processes to maintain and improve upon current standards. Predicting future trends requires examining current innovations and extrapolating potential applications.
Emerging Technologies
Emerging technologies hold significant promise for enhancing high-end water resistance. Nanotechnology, for instance, allows for the creation of incredibly thin and highly water-resistant coatings. These coatings, often incorporating self-healing properties, could dramatically improve the long-term performance of water-resistant materials. Additionally, advancements in 3D printing are enabling the production of intricate, complex designs with enhanced water-tight seals, potentially leading to more streamlined and efficient designs.
Advancements in Materials
Materials science is a crucial driver of innovation in high-end water resistance. Novel polymers, composites, and ceramic materials are being developed with enhanced water-repellency and durability. These new materials often exhibit superior resistance to corrosion and degradation, critical for prolonged performance in harsh environments. For instance, the development of advanced polymer blends with incorporated ceramic nanoparticles has shown promise in creating stronger and more water-resistant materials compared to traditional polymers.
Advancements in Manufacturing Processes
Innovative manufacturing processes are crucial for realizing the full potential of advanced materials. Laser-based techniques are becoming more sophisticated, enabling precise and intricate sealing procedures for complex geometries. This allows for the creation of tighter, more reliable water barriers within products. Similarly, advancements in surface treatment technologies allow for the application of ultra-thin, highly water-resistant coatings, which are crucial for maintaining high-end aesthetics while enhancing performance.
Impact on the Market
These advancements will significantly impact the high-end water resistance market. Consumers will likely demand products with enhanced durability and performance, leading to a greater emphasis on innovative materials and sophisticated manufacturing techniques. The market will likely see a premium placed on products utilizing cutting-edge technologies, reflecting the value of advanced water-resistance capabilities.
Predicted Future Trends
The following table Artikels predicted future trends in high-end water resistance:
Trend | Description | Impact |
---|---|---|
Nanotechnology-based coatings | Integration of self-healing and highly water-resistant nanomaterials into protective coatings. | Increased durability, reduced maintenance, and improved aesthetic appeal. |
3D printing for intricate seals | Use of 3D printing to create complex, water-tight seals in high-end products. | Enhanced design flexibility, improved performance, and potentially reduced manufacturing costs. |
Advanced polymer composites | Development of novel polymer composites with enhanced water resistance and corrosion resistance. | Increased product longevity, suitability for diverse applications, and potential for lighter-weight designs. |
Laser-based sealing | Refinement of laser techniques for precise and intricate sealing, especially for complex designs. | Improved sealing quality, reduced material waste, and enhanced aesthetic appeal. |
High-End Water Resistance in Different Product Categories
High-end water resistance is no longer a niche feature but a critical element in various product categories. From luxury watches to sophisticated electronics, consumers demand durable and reliable protection against water damage. This necessitates innovative design and manufacturing processes to achieve exceptional water resistance levels. This exploration delves into the specific demands and implementations of high-end water resistance across diverse product categories.The varying applications of high-end water resistance necessitate tailored design approaches.
For example, a watch must withstand water pressure for extended periods, while a high-end smartphone might require splash-proof capabilities for everyday use. The degree of water resistance and the specific mechanisms for achieving it differ significantly across these categories.
High-end water-resistant phones are a must-have for adventurers and those who just want peace of mind. Pairing that with the convenience of a best dual SIM phone for staying connected while traveling or managing multiple numbers is a solid choice. Ultimately, the top water-resistant phones offer both reliability and flexibility.
Watches
High-end watches often prioritize extreme water resistance for both aesthetic and practical reasons. They frequently employ intricate designs to ensure sealing and protection against water intrusion. The use of high-quality, corrosion-resistant materials like titanium and sapphire glass is crucial. Furthermore, the meticulous sealing around the crown and case back plays a vital role in maintaining water resistance.
For example, some high-end dive watches are capable of withstanding pressures equivalent to depths of several hundred meters.
Clothing
High-end water-resistant clothing, such as rain jackets and outerwear, prioritizes breathability and comfort in addition to water resistance. Advanced fabrics, often utilizing micro-porous membranes, are key to achieving this balance. The goal is to keep the wearer dry while allowing perspiration to escape. This often involves intricate material constructions and specialized coatings to repel water while maintaining breathability.
Electronics
High-end electronics, including smartphones and cameras, require high-end water resistance to withstand splashes and accidental submersions. The focus is on sealing critical components, such as ports and connectors, to prevent water from reaching sensitive electronics. Modern technologies, such as specialized gaskets and waterproof coatings, play a crucial role in this endeavor. For example, certain high-end smartphones boast IP68 or higher ratings, indicating their resistance to water ingress under specific pressure and duration conditions.
Table: High-End Water Resistance in Different Product Categories
Product Category | Water Resistance Features | Specific Applications |
---|---|---|
Watches | High-pressure resistance, meticulous sealing, corrosion-resistant materials, precise craftsmanship | Dive watches, luxury timepieces, professional applications |
Clothing | Water-repellent fabrics, breathable membranes, specialized coatings | Rain jackets, outerwear, high-performance apparel |
Electronics | Specialized gaskets, waterproof coatings, sealed ports, connectors | Smartphones, cameras, high-performance audio equipment |
Wrap-Up
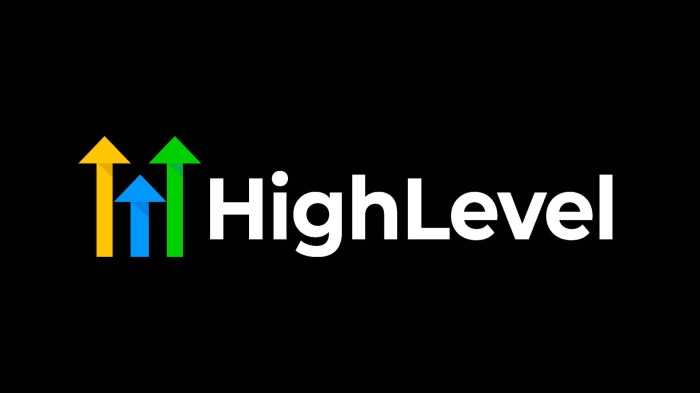
In conclusion, high-end water resistance is more than just a feature; it’s a testament to meticulous design, advanced materials, and rigorous testing. This exploration has highlighted the diverse applications and the specific requirements for achieving top-tier protection in various products. The future of high-end water resistance promises further innovation and even more robust solutions.
Q&A
What are some common materials used in high-end water-resistant products?
High-end water-resistant products often utilize materials like titanium, ceramic, sapphire glass, and advanced polymers, known for their strength and durability against water pressure.
How do different testing methods ensure high-end water resistance?
Testing methodologies involve submersion tests, pressure simulations, and exposure to various environmental conditions, all designed to rigorously evaluate a product’s water resistance capabilities under different scenarios.
What are the environmental concerns related to high-end water-resistant materials?
Some high-end materials, while durable, may have environmental concerns. The focus is shifting towards using sustainable alternatives where possible.
What are some innovative manufacturing techniques for high-end water resistance?
Innovative manufacturing techniques include advanced sealing processes, precision molding, and the use of specialized adhesives, all contributing to consistent and reliable high-end water resistance.